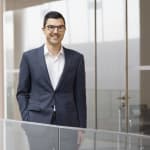
Interview with Dr. Stefan Engleder, CEO of Engel Group.
The rapid development of digital technologies has widely opened the gate to the era of the so-called Industry 4.0. What impact does digitalization have on the injection molding machine industry and how has it changed the approach to injection molding processes?
Digitalization is radically changing our production methods. This is comparable with the transformation in the automotive industry. Vehicles will be autonomous in the future, and injection molding machines will self-control and self-optimize themselves independently.
Digitalization is already a decisive competitive factor today. Industrial production processes are becoming increasingly complex. But digitalization can help to manage and control them in an easy and safe way. Digital solutions make it possible to leverage the full potential of injection molding machines and optimize production processes on the basis of the generated data. As a result, quality, productivity and efficiency are rising significantly. Digitalization is the prerequisite for sustainability. We will only be able to achieve the given CO2 reduction targets if we consistently take the opportunities offered by digitalization.
But these are still the beginnings of advanced digitalization and, generally speaking, the level of maturity in terms of the digitalization of injection molding processes is still heterogeneous.
That's right. If we look at the massive potential that digitalization opens up, we are still at the beginning of this development and the differences in how production processes are being digitalized in the enterprise are substantial. On the one hand, this is due to the fact that, just like with capital expenditure on new machines and production units, digitalization projects are also precisely adapted to individual requirements. The focus is always on the concrete added value for the user. On the other hand, we also see some companies still struggling with the decision to invest in digital solutions, even though the benefits are obvious. We would be happy to see more trust in the new solutions here. What it will take is a change in the mindset. We are actively pushing for people to leverage the opportunities that digitalization opens up and to gear their injection molding production facilities for future requirements with a view to competitiveness, but above all to sustainability. A wide range of both field-proven and new digital solutions is available for all maturity levels.
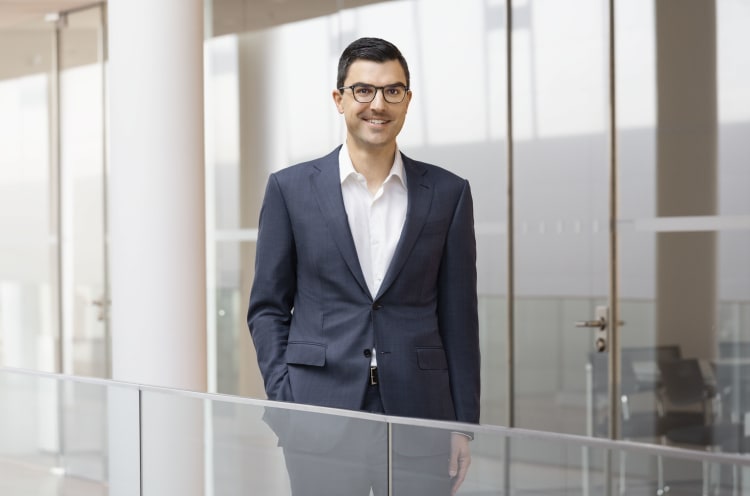
Dr. Stefan Engleder, CEO of Engel Group
Well, let's say what doors digitalization opens – what specific opportunities it makes available.
As previously mentioned, digitalization helps us to leverage the full potential of the injection molding machine or systems solution, and to make production more efficient and avoid rejects by doing so.
For example, sim link, the interface for exchanging data between the simulation program and the injection molding machine, has already helped us to lay down the tracks for a sustainable manufacturing process, and for recycling later on, during the development of the product. The iQ weight control smart assistance system, to cite another example, makes it possible to use recycled material even in processes for which virgin material was previously unavoidable.
On top of this, the lack of qualified personnel is also driving our clients to invest in digital solutions. It's all about supporting production personnel and ensuring a consistently high product quality, even if skilled personnel is not available on every shift.
As injection molding processes become increasingly digitalized, the volume of data is increasing. Data contains a lot of information but this is often not recognizable at first glance. How does using this information support processes optimization?
This definitely is one of the greatest challenges, extracting information from the increasing volume of data to support both process and production optimization and troubleshooting. Data scientists are trained precisely for this task. However, only very few processors employ their own data experts. This is why ENGEL now offers this expertise as a service following the addition of our new "analytics" package in our performance.boost process optimization service. We have built up personnel resources for this. Our data scientists have years of injection molding experience on top of well-founded data analytics training. They understand the injection molding machine and the processing technologies, and that is precisely the major advantage of performance.boost analytics compared with other service offerings on the market.
Our data scientists systematically analyze the available data for each specific use case, visually process the results and develop concrete recommendations for action. For example, to increase production efficiency or reduce the reject rate. Depending on the application and customer requirements, the production and process data as well as data from quality assurance deliver the raw data, which is collected over a longer period of time. The analysis allows insights into the root causes of rejects, for example, reveals gradual quality changes and enables long-term trend statements.
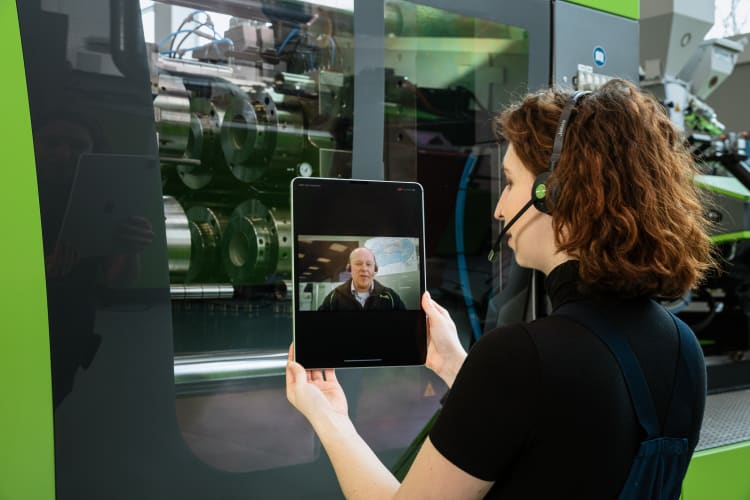