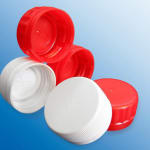
The closure design PCO 1881 was launched in 2008. Since then, numerous versions have come into use. What is impressive about this is that the weight of the closure has been continually reduced: originally 2.45 grams when launched, it is now 2.3 grams for carbonated soft drinks and up to 1.8 grams for still water. These savings are also necessary in view of growing capacity, as several thousand tons of raw materials can now be saved each year. So what contribution can machine manufacturers make to this development?
In order to meet growing capacity as far as the machines are concerned, technical advances in the performance data of the injection unit, clamping unit and main drive are required.
In terms of the injection unit, it is the plasticising performance in particular that must be taken into account. In order to do this, Netstal is furnishing the ELION and EVOS series with the tried-and-tested barrier screw and the new unit sizes 1000, 2000 and 2900. The combination of high-performance screws and high-torque screw drives makes it possible to dispense high shot weights from a Netstal machine in the shortest possible time and with excellent melt quality. The PE-HD types used as standard with an MFI (Melt Flow Index) of less than two can also easily be processed in the same way, such as the newly emerging bimodal and multimodal grades.
In addition, the injection piston sizes were revised in order to achieve the same injection performance with lower oil volumes. The reduced oil consumption has a direct impact on the drive size and therefore energy consumption. Thanks to the improved performance of the EVOS / ELION injection moulding units, the hybrid 2000M unit can now be used instead of the hydraulic 2150 unit.
Different measures have been employed with regard to the clamping unit and drive in order to achieve the objective of reduced energy consumption. Priority should be given first and foremost to the selection of the right drive technology. The ELION and EVOS series offer optimum combination options to reduce energy consumption.