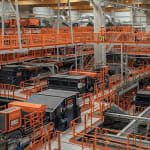
The high-tech TriPlast sorting plant in Ennshafen has been making a significant contribution to the Austrian circular economy since it went into operation a year ago - and is exceeding expectations. Now the owners Altstoff Recycling Austria AG (ARA), Bernegger and GreenDot developing a new 35 million euros investment plant, which is being built at the same Ennshafen site and will take plastics recycling to a new level. The Upcycle process, developed and patented by ARA, will be used to process up to 41,000 tons of sorting waste plastic every year. The aim is to supply even more high-quality recyclates, including for sensitive applications such as food packaging, in order to strengthen the circular economy and raw material security in Austria and Europe.
By the end of next year, TriPlast is to be enriched by an innovative new feature: The technological centerpiece is the Upcycle process developed and patented by ARA for the enrichment of polyolefins, which is already being used in a pilot plant in Pöchlarn, Lower Austria. This means that the sorting plastic residues from the TriPlast output as well as additional quantities from other sorting plants that could previously only be used as substitute fuel - e.g. because they are too contaminated or too small - can be further processed. This increases the yield and recycling rate. The system also offers a solution for processing composite beverage cartons (PolyAl). With the help of upstream fine sorting, individual plastic fractions can also be cleaned in an even more targeted manner to subsequently supply recyclates for high-quality applications: the enriched polyolefin fraction is intended to be suitable for use in the food sector through chemical recycling or even, in the future, through mechanical recycling. The expansion will enable up to approx. 41,000 tons of sorting residues to be further processed.
1 year of TriPlast: original yield of 80% has been increased to 85%
The high-tech TriPlast sorting system is designed to sort 20 tons of material per hour from the Yellow Bag or Yellow Bin, i.e. around 100,000 tons per year. The results after one year of operation have exceeded expectations: the original yield of 80% has been increased to 85%.
“TriPlast is a compelling best practice example for cross-border circular economy initiatives,” says Laurent Auguste, CEO of GreenDot. “We firmly believe that strong partnerships built on pooled expertise can make a decisive contribution to Europe's resource independence. TriPlast demonstrates how innovation, technology and collaboration can set new benchmarks in waste utilization. With our long-standing experience in system leadership, we are developing solutions that are both environmentally and economically sound, and that directly support our brand-owner customers in meeting the rising recycling targets outlined in the new EU Packaging and Packaging Waste Regulation.”
"With TriPlast, we are once again living up to our reputation as a driving force in the Austrian recycling industry - and we still have big plans. With a yield of an impressive 85%, we can provide even more material for the recycling process. The aim must be to subsequently recycle these quantities as completely as possible. By investing EUR 35 million, we are expanding the plant with our patented Upcycle process and turning the Ennshafen site into an even larger innovation center for the circular economy," explains Thomas Eck.
Since its official launch on July 1, 2024, TriPlast has not only operated smoothly but surpassed expectations. Its sensors detect 24 different waste fractions, analyze and sort them by type, enabling state-of-the-art separation. A diverse team of 70 employees works on-site in service of the circular economy. “It pays off to pull together daily as a joint venture - for waste management, Austria’s economic future, the environment, and the climate,” adds Kurt Bernegger, CEO of Bernegger GmbH.