CARD – small dryers with a great effect
The new compressed air dryers from the CARD series have been an integral part of the Wittmann product portfolio since April 1 of this year. The first few months have shown that, in spite of the great variety of different models and sizes, three types of appliances have become particularly popular. These are the sizes CARD 6G/FIT, CARD 10S and CARD 20S. On these appliances, the desired drying temperature can be set via a touch screen operating panel, and at the end of the pre-drying phase a signal is issued to release an automatic production start-up. The material drying data can be exported via a USB port or via OPC UA.
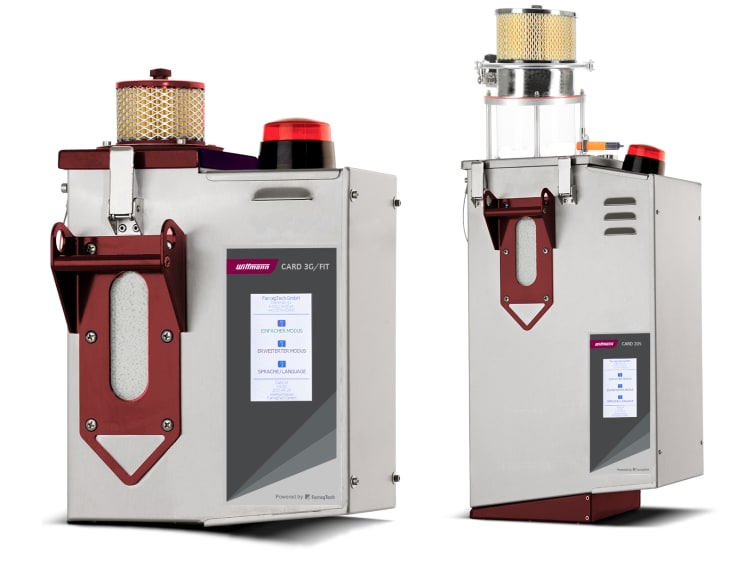
CARD G (left) and CARD S with FIT control system and optional OPC UA interface.
With the integrated week timer, the use of the dryers can be ideally adapted to ongoing production planning, and they are ready to run immediately as soon as dried material is required. In the CARD S models, the compressed air consumption is very finely and precisely adjusted to the actual demand by an intelligent digital air volume control system.
If a material loader is used to fill the dryer, this ensures a continuous material supply, and the dryer recognizes automatically when the drying temperature must be lowered.
If the interval between two conveying cycles exceeds a certain period of time, this is interpreted as “no material consumption”, and the dryer then starts the necessary actions to protect the material and to reduce energy consumption.
CARD dryers can be mounted directly onto the machine feed. In combination with a claw flange, the appliances can be pushed into a parking or emptying position.
If quick-change adapters are used on CARD dryers, this will save time when transferring the dryers from one machine to another.
TEMPRO plus D120 temperature controller
The response to the introduction of the single- and dual-circuit variants of the pressurized TEMPRO plus D100 appliance last year have far exceeded all expectations. In the feedback, the desire for a pressurized appliance of similar size with direct cooling was expressed again and again. To meet this demand, Wittmann has now developed the new TEMPRO plus D120 temperature controller, also in a single- and a dual-circuit version.
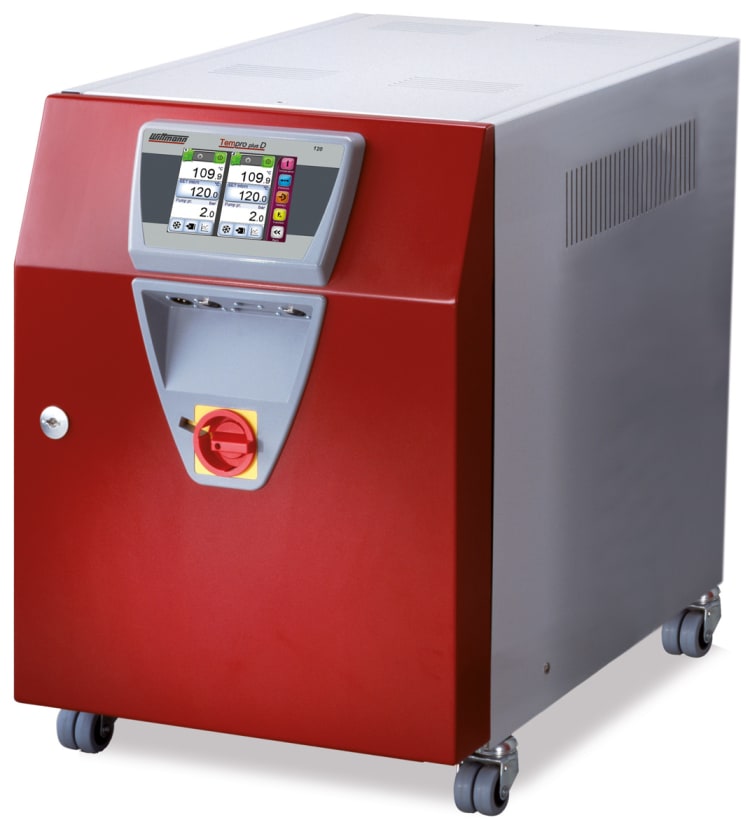
Witmann TEMPRO plus D120 pressurized temperature controller with direct cooling.
Although its extensive standard equipment package is already impressive, the TEMPRO plus D120 will certainly leave no configuration wish whatsoever unfulfilled when combined with the available optional extras.
- TEMPRO plus D120 has a direct cooling capacity of 80 kW with a Δt of 75 °C as standard.
- The standard heating performance of 9 kW can be increased to 12 kW or 16 kW if a higher production temperature is required.
- The available choice consists exclusively of stainless steel pumps with wear-free magnetic couplings to accommodate maximum flow volumes ranging from 40 l/min to 90 l/min. A real specialty is the frequency-controlled pump model with a capacity of 1.1 kW / 50 l/min / 9bar. The advantages of having this pump model installed in a temperature controller are the differentiated options for parameter setting in terms of motor speed, pressure and flow volume. This enables users to decide for themselves by which parameter they wish to have their process regulated, and last not least with a view to energy saving potential.
- In the era of digitally connected communication media, an interface via which numerous process parameters can be exchanged with all well-known brands of injection molding machines is an absolute must. So the new EUROMAP 82.1 interface is available for the TEMPRO plus D120 as an option, and use of the OPC UA protocol as well. Wittmann and Wittmann Battenfeld are pioneers in “one-stop shopping”, and as such also very well prepared for comprehensive digital communication of all components with each other in a production cell via the standard Wittmann 4.0 interface.
The range includes many additional options to meet the requirements of every customer-specific application, with all conceivable equipment variants being available for both 1-circuit and 2-circuit models – of course with dimensions doubled for every 2-circuit version.