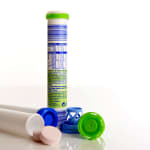
Sanner, manufacturer of pharmaceutical primary packaging and medical technology products, is investing in the expansion of its in-house tool and mold making. This enables the company to ensure rapid delivery of standard products that are in high demand especially in times of pandemic, such as desiccant closures and nutritional supplements packaging. However, the investments are also paying off in the development and implementation of new products and will be consistently continued in 2021.
The corona pandemic has changed production at Sanner significantly: the DASG 1 desiccant closure in particular has seen a 30 percent increase in demand. The DASG 1 is Sanner's classic spiral closure, which is only original with five fingers and Sanner undercuts for the guarantee function. A short delivery time is crucial, especially for such standard products. "In order to ensure this delivery time even in times of high capacity utilization, we already decided to continuously expand our own tooling technology several years ago," says Dr. Johannis Willem van Vliet, Managing Director of the Sanner Group. "This now allows us to respond much faster and more efficiently to changing customer requests in times of Covid-19."
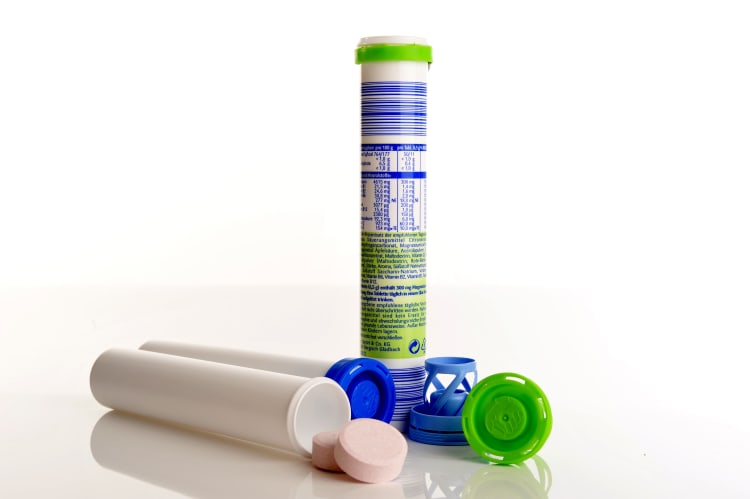
The classic DASG 1 desiccant closure in particular saw a 30 percent increase in demand in 2020.
Physical and technical proximity to production
Beyond the pandemic and the increased order intake, the physical and technical proximity to production is a priority for Sanner. In the past five years, the company has invested around two million euros in tooling technology. Purchases in 2020 included a new eroding machine to produce sharp and precise internal contours, as well as a surface grinding machine for the final finish of the mold inserts.
With three new injection molding machines, Sanner has already significantly expanded production and capacity for nutritional supplement packaging in 2020. Thanks to its well-equipped in-house tool making, the company can quickly and easily produce its own molds with multi-stage cavity designs for these and further new machines that are planned for the first half of 2021 due to the increased demand. "Our customers have the certainty that all molds are ideally optimized for both machines and products," explains Thomas Ergler, head of tooling technology at Sanner. "This, in turn, enables us to ensure smooth production with low reject rates at the highest quality."
"Automation and digitalization are becoming increasingly prevalent in tooling technology and are generating savings," says Ergler. For example, the entire tooling technology organization is IT-supported, including the automatic tool dispensing system. In addition, a wide variety of geometries can be created quickly and precisely on the processing center thanks to integrated five-axis simultaneous operations.
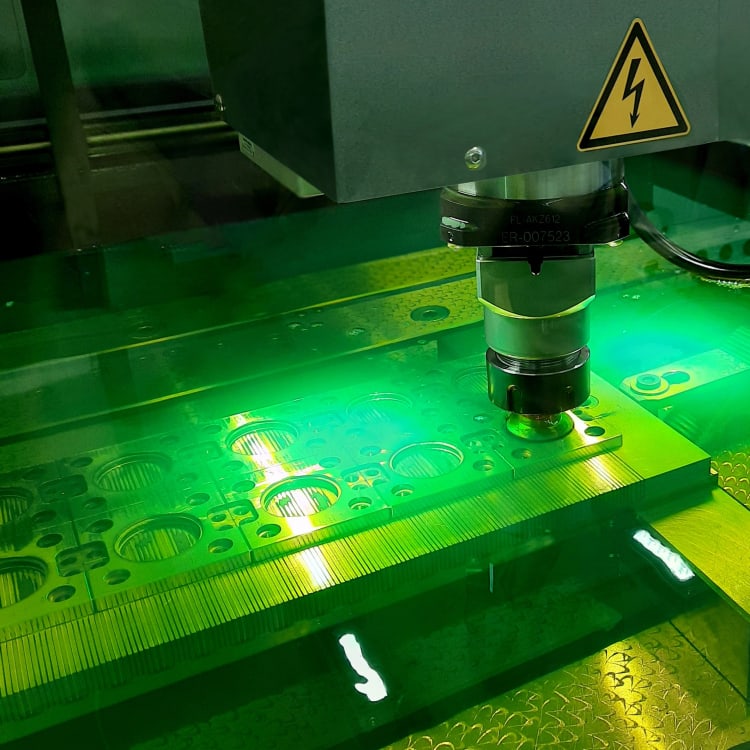
Sanner_eroding: Sanner's investments in tooling technology also include the eroding machine purchased in 2020.
Supporting product development
In-house tooling technology essentially comprises tool processing technologies such as milling, turning, grinding, eroding, and measuring. They are not only important for existing products; they also provide efficient ways of analyzing and methodically developing new materials and technologies. For example, tooling technology supported the Sanner experts in the market launch of Sanner BioBase, the first effervescent tablet packaging made of bio-based material.
"As early as the development process, our interdisciplinary team of experts can methodically test the feasibility of potential new products," explains van Vliet. "This saves us and our customers a lot of time and money." Accordingly, Sanner is planning further investments this year.