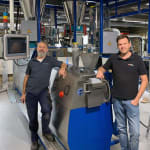
The company Nexam Chemical AB from Lomma, Sweden, was looking for a new compounding plant that could be used specifically for the production of reactive masterbatches. The machine manufacturer Feddem GmbH & Co. KG based in Sinzig, Germany, supplied the suitable plant and encountered some challenges in the process.
With the new compounding line at the Lomma plant, Nexam aims not only to produce its current product range more efficiently, but also to develop new types of reactive masterbatches for its existing and new customers. A special requirement here is the production of so-called ATEX materials (explosive atmospheres), which required special consideration of safety measures and adaptation of the extrusion line. Another constraint was the limited space on the plant side due to the existing metal structures in the building.
The cooperation between Feddem and Nexam began with trials at the masterbatch manufacturer AF-Color, which, as a branch of Akro-Plastic GmbH, is a member of the Feddersen Group, just like the machine manufacturer. These trials offer the customer the opportunity to test products or formulations on the machine builder's equipment that is already in the production process. Subsequently, it is possible to validate formulations and their mechanical properties, such as modulus of elasticity or notched impact strength, in the laboratory.
"Thanks to our ICX technology, a standardised machine concept, we were able to guarantee the customer a functioning production process for his products on a small extrusion line with low costs and fast set-up times. This technology enables us to make subsequent scale-ups to implement the required throughputs or individual adjustments to the subsequent production line without running the risk of losing batch consistency in the final line," explains David Constroffer, head of project management at Ffeddem. According to the machine manufacturer, this not only saves machine capacities in the test planning, but also material in the test execution. Especially with cost-intensive products, the iterative procedure for tests can be carried out in a cost-reducing manner.
Within a few weeks, the project management and design & development departments at Feddem worked out a plant concept to meet the customer's requirements. In close coordination with Nexam, it was possible to transfer the special requirements from the production of ATEX materials, the limited installation space and a very tight schedule to the final production line.
Based on the required throughputs and formulations, the extruder type FED 52 MTS 36 L/D was chosen. 36 L/D indicates the housing length. Here, the customer's wish was taken into account that an additional housing would make it possible to add liquid additives by means of an injection nozzle.
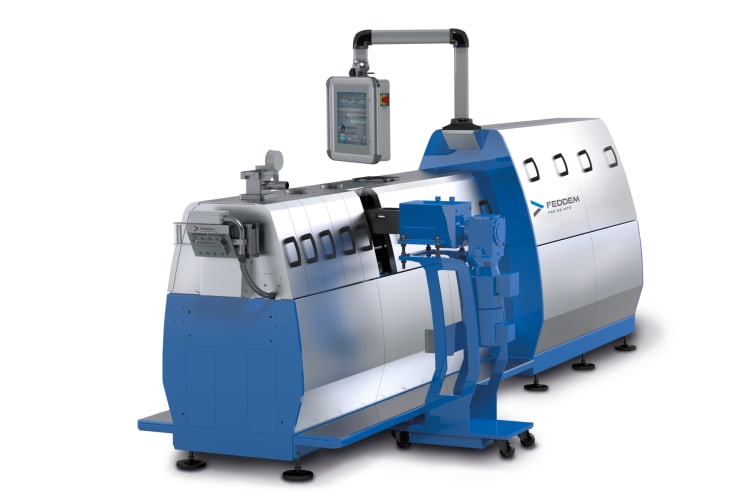
After commissioning and acceptance of the production line with two FSB side feeders, the dosing system for raw materials, vacuum system and cooling system, Dirk Breuer, service technician at Feddem, conducted training for the operating staff on site in Lomma. During this training, the first batches of the customer's product were already produced.
"A big thank you for the great cooperation with the entire Nexam team and a special thanks to Jörgen Heby and Sebastian Holm, with whom we were able to realise this project," adds David Constroffer.