Profiting from commodity recovery
With 20,000 ft2 under roof for tipping floor space, Alan Coulter, general manager for MarBorg Recovery, operator of the Resource Center’s MRF, says space is tight. “We can’t keep material sitting on the floor for too long. We must keep it flowing from the floor to the circuit,” he says.
Poiesz mentions the automated sorting circuit’s designed capacity is 1,000 tons per day. “We currently run, on average, 800 tons per day of both MSW and single stream,” adds Brandan Fix, operations manager for MarBorg.
The screening process also separates overd material greater than 14 in, diverted from the automated circuit for manual sorting. “Our goal is for quantity of material removed from the stream, so we employ manual sorters to help maximize material recovery,” offers Coulter. Johnston further explains, “We have a 60% contracted diversion rate from the landfill for MSW material.”
The remaining 2.5- to 14-in waste material is sent through a series of 10 Tomra Autosort units for recovery of valuable recyclable commodities, including plastics, plastic film, paper and wood. Ty Rhoad, regional director Americas for Tomra Recycling Sorting explains, “MSW contains valuable secondary raw materials. If they are recovered through mixed waste sorting and further recycling, we take circularity and greenhouse gas (GHG) benefits to new heights.”
Johnston mentions the landfill is benefiting from the circuit’s designed flexibility. “Van Dyk was hired because they have better equipment, and I believe the Tomra units are better sorters,” he says.
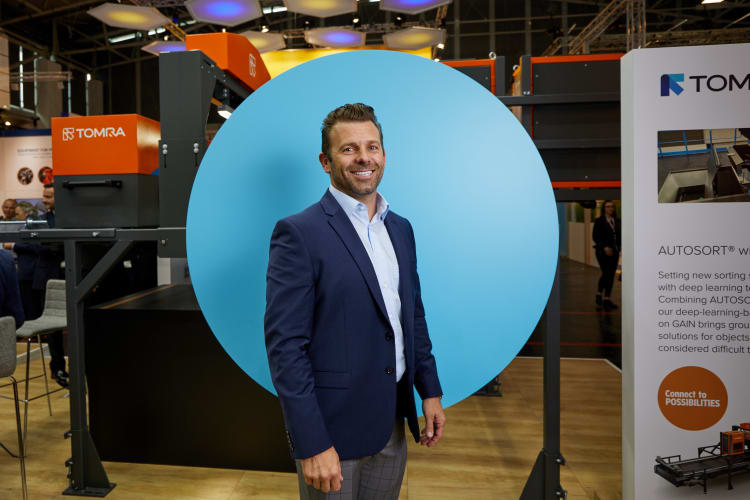
As a preferred supplier for Tomra sorting technology in North America, Van Dyk has extensive experience incorporating flexibility into their system designs. The recovery facility’s designer and installer focuses on “future proofing” MRFs, helping them to adapt to market changes both today and many years down the line. The facility was designed to be able to capture any commodity to keep up with the evolving tonnage. To confirm this point, Johnston adds, “We are now recovering a PP#5 product for sale, and that market didn’t exist when the facility was in development.”
Compact and highly flexible, the Tomra Autosort multifunctional sorting system can be used across a range of material sorting applications, including MSW, single stream, plastics, and E-Scrap. The new generation Autosort incorporates the latest Tomra technologies to offer advanced accuracy of complex sorting tasks, such as pulling recyclate from MSW feed material, at high throughput rates.
Using near infrared (NIR) and visible light spectroscopy (VIS) to identify objects, Autosort’s Sharp Eye technology increases light efficiency while maintaining the same energy consumption to advance sorting sharpness and improve separation of difficult to target fractions. The sorters also include TOMRA’s patented Flying Beam sensing technology to offer better light efficiency, flexible and easy installation, and enhanced light signal efficiency for improved detection.
Combined, Sharp Eye and Flying Beam help to consistently deliver high performance sorting accuracy across all target fractions. “Automation and the Tomra sorters are the most consistent part of the operation,” comments Coulter.
Van Dyk designed the Resource Center’s circuit to use a positive sort, where the desired recyclable material fractions are ejected by the valve blocks, to increase recovered material purity. Each Autosort unit is equipped with three to four different “recipes” of materials that operators can select to recover from the unit.
“Autosort can be configured with dozens of recipes for recovered materials. Tomra collaborated with Van Dyk to configure the sorters according to the customer’s needs, and then Van Dyk installed the units, programming them with the required recipes,” offers Parker Bynum, western area sales manager for TOMRA Recycling Sorting. Fix adds, “We are impressed with the flexibility of programming to quickly change recipes to fire on different material.”