
Nowadays, plastics and synthetic fibres are widely used in every area of technology, and enter into every aspect of our daily lifes. Although they are not naturally occurring materials, they have become of everyday use, even in manufacturing of valuable objects, which are now completely familiar.
Until a few decades ago a "plastic" object, or a clothing made of synthetic fiber, communicated the feeling of a mass-produced product, certainly functional, but not always synonymous of high quality. Today, the technological evolution of plastic polymers and their technical and aesthetic characteristics has reached levels that were unthinkable until some time ago.
The era of plastics began with the processing of Bakelite and celluloid. However, the plastics market has evolved rapidly to meet the needs of an increasingly demanding customer base.
The plastic material should be properly heated and dehumidified for a correct processing and to improve its aesthetic and mechanical strength properties. For this purpose, in the early 1970s, a container with a truncated-conical shape was created for the dehumidification treatment process. The impacts of the dehumidification process on the quality of the final products have been underrated for long by a fast-running market that lacked the technical expertise to analyse them.

OTX (Original Thermal eXchanger), the drying revolution
Moretto guessed that dehumidification was a key factor in achieving a stable moulding and extrusion process, one that could guarantee performance under control and in line with the required parameters. It was therefore necessary to examine the behaviour inside the hopper to significantly improve system performance.
Extensive studies began about 30 years ago, and through software for "discrete element" analysis, introduced in 2007, a series of experiments were carried out to evaluate granule by granule the path through the traditional hopper. The analysis showed that with these hoppers, it was not possible to guarantee the release of properly dehumidified material, as it could not be ensured that all granules met the required residence times.
Also involving the university and external engineering consultants alongside the company's R&D department, and through targeted investment, Moretto investigated the "hopper" issue, jointly analysing the geometry, fluid dynamics and thermodynamics of the system. The Leonardo supercomputer, capable of 22 trillion operations per second, allowed the system to be mapped from different points of view. These analyses disassembled the process as a whole, highlighting areas for possible improvement.
Moretto completely rethought the internal and external geometry of the hopper, developing OTX (Original Thermal eXchanger), which revolutionized the dehumidification process and the concept of the hopper itself, realizing a real exchanger between energy and humidity, with extraordinary energy efficiency.
Drying time is reduced by 40% and, for the same throughput, the hopper volume decreases by 40%. In addition, thanks to the unique internal geometry and maximum attention to detail, energy efficiency is improved by 66%, significantly reducing the costs of such an energy-intensive process as dehumidification. Incredible results that represent a huge competitive advantage when compared to conventional hoppers!
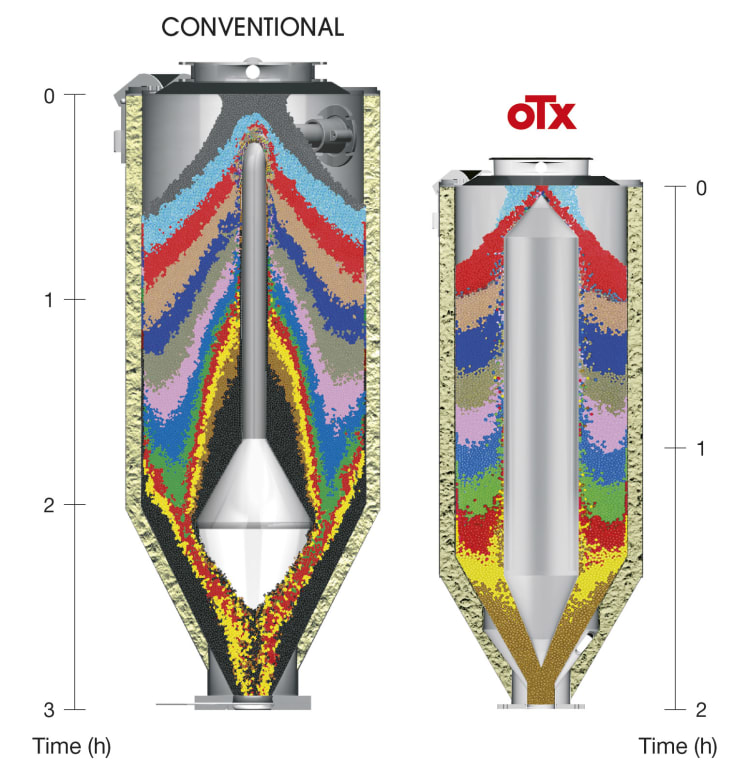
Comparison between a conventional hopper and OTX
Evaluating the current electricity costs, this system guarantees a return on investment in less than two years.
Each hopper is equipped with a viewer that provides the drying status of the material and the temperature display, so that the working condition of the machine is known at all times.
Some competitors are keeping a conventional approach to the subject of dehumidification as they are not aware of the developments that have been possible thanks to calculations made through artificial intelligence. Moretto's OTX hopper is an exclusive product protected by 7 patents that has made a revolution of technical polymers dehumidification, securing the company a leading position in terms of energy efficiency, competitiveness and high-quality performance.