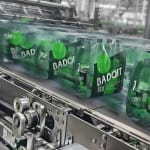
First-class natural mineral water and an exclusive bottle design are the trademarks of the Badoit spring. From the bottled water to the packaging the premium brand makes the highest demands of the quality of its products. KHS has supported the company, part of Danone, since 1986. With its new Innopack Kisters SP A-H shrink packer Badoit is again benefiting from the expertise of the Dortmund machine and systems manufacturer. The packaging machine produces shrink film processing quality as yet unrivaled on the market with practically crease-free and consistently stable results.
France is heralded as a paradise for gourmets. The land of haute cuisine is renowned the world over for its award-winning wines, outstanding cheeses and high-class natural mineral waters. One brand which has established itself as a leader among carbonated natural spring waters is Badoit. The bottler from Saint-Galmier in the Département de la Loire, southwest of Lyon, has been working closely with the country’s top restaurants for many years. In doing so Badoit has earned itself a reputation as a top brand of high-quality mineral water in the premium sector. “Our customers make the highest demands of our products – and not just regarding our water. The perfect quality of the packaging also plays a decisive role,” says Etienne Marie, plant manager at Badoit.
The premium market: packaging quality plays a key role
Not only on the home market is the design of primary and secondary packaging a marketing factor which determines the product’s success. “Beverage brands can clearly position themselves on the market through the nature of their presentation and design,” explains Christopher Stuhlmann, head of the Line Product Division at KHS.
This aspect is especially important for Badoit. “As a premium brand our products not only have to differ from those of the competition in quality but also in appearance. The exclusive standard of our water must also be reflected in the packaging,” states Marie. The mineral water plant has therefore opted for bottles with a long, elegant neck, a unique feature on the French market.
Badoit requires better packaging quality
While the unusual bottle shape is a blessing when it comes to brand recognition, it has proved quite a challenge for the shrink packers used by the water bottler – also for its KHS Kisters packaging machines, some of which have been in operation for over 30 years. “The long-necked bottle makes it extremely difficult to produce a packaging quality which is outstanding in all respects,” Marie says. “The multipacks often had creases in the film, the print was distorted or the packs weren’t stable enough to withstand the logistics.” In addition, the outmoded packaging machines were no longer state of the industrial art when it came to efficiency and sustainability and were increasingly limited in their technological capacity. “We were no longer able or prepared to accept these compromises in packaging quality and machine efficiency,” claims Marie.
Badoit received support from its parent company. Danone Waters launched a competition between its individual brands and their production plants who then turned to their respective suppliers. “Danone Waters wanted a packaging machine which, thanks to significant further developments in the shrink tunnel segment in particular, considerably improves the standard of the shrink film processing available to date,” emphasizes Stuhlmann. Here, it was especially important that the lettering and brand logo on the packs was neither distorted nor creased.
KHS beats the competition
Following intensive talks on the new specifications to be adhered to and the first promising tests KHS was ultimately awarded the contract for the project. “We have a close and trusting relationship with KHS. Its many years of expertise in the development of packaging systems and the strengths of its latest generation of machines had us convinced once again,” is how Marie describes the reason for choosing KHS.
The systems supplier now had to live up to these high expectations. Under the supervision of Christian Schilling, head of the shrink tunnel development group at KHS, the machine and systems manufacturer put together an experienced team of design engineering experts. They were in close contact with the engineers in Saint-Galmier. “Throughout the course of the entire project the teams worked together openly and absolutely professionally as partners – as usual,” Stuhlmann reports.