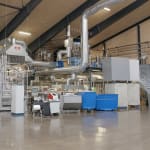
“We always keep a step ahead of the market. We don’t do things by halves,” is the motto of Jacob Sörensen, Managing Partner of the Danish company Staal og Plast A/S. A glance into the production halls in Ringe impressively underscores his statement. Here stands the world’s largest thermoforming line with a footprint of 20 square meters, which transforms about 3 mm thick, extruded, HI-semi-finished PS sheet into what is known as ebb & flow trays for greenhouseshothouses. To produce the up to 8 m long and 2.5 m wide semi-finished boards, battenfeld-cincinnati Germany, Bad Oeynhausen, installed an ultra-modern sheet extrusion line with throughput rates of up to 3,000 kg/h just under a year and a half ago.
In addition to the rising world population and the resulting added demand for flowers, shrub and vegetable seedlings for professional and amateur gardeners, fresh herb pots for modern kitchens and the increasing cultivation of cannabis are all contributing to the booming greenhousehothouse construction. The Danish company Staal og Plast supplies precisely this niche market with made-to-measure high-impact polystyrene (HIPS) trays. The company, founded in 1984 by the father of today’s Managing Partner, concentrated right from the beginning on greenhousehothouse products, which during the first years included steel profiles as well as plastic trays, as the company’s name suggests. “Today, we process exclusively plastics, since we are convinced that this is our core competence”, explains Jacob Sörensen. “We are concentrating on what we can do best, which means on just one product.” Obviously a concept which makes sense, for the relatively small company with just 15 employees makes 60 to 70% of all sheet products required for greenhouseshothouses worldwide. And the market leader continues to grow. This is why it increased its production capacity at the Danish facility fourfold with the installation of the high-speed line and established a subsidiary in Chicago/USA, equipped with a thermoforming line to start with. “Especially in North America, there is an enormous demand for our so-called ‘Danish trays’. The reason is the increasing cultivation of cannabis, which is not only grown for medical purposes, but due to its legalization in several federal states also more and more in demand for leisure applications”, explains Jacob Sörensen, suggesting that he may further expand his overseas facility in the near future and install an extrusion line there, too. Until that time, the company will continue to transport its Danish trays to the United States to have them thermoformed locally. “This is the only way we can guarantee our high quality standards to our customers.”
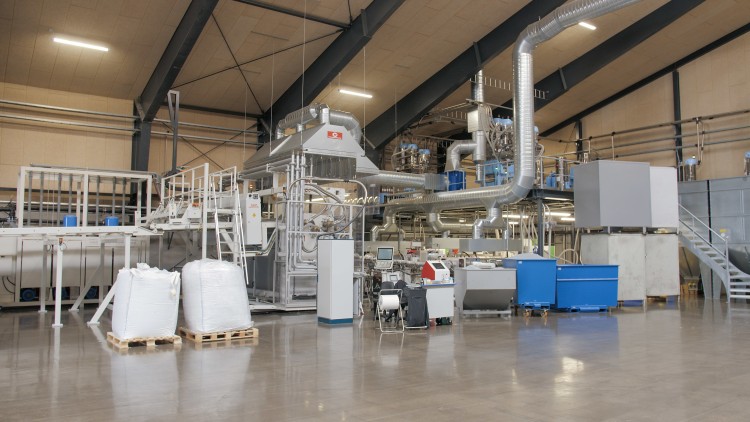
High quality standards and …
For the 3-layer sheet line from battenfeld-cincinnati installed in 2018, Staal og Plast first built an entirely new hall to house the line with a total length of 65 meters and also to provide enough space for the huge thermoforming machine and extra space for handling the largest boards, which measure 2,500 by 8,000 mm. In the new co-extrusion line, the high-speed extruder 1-75 T6.1 is responsible as main extruder for the total capacity of up to 3 t/h. It alone reaches an output of about 2 t/h for HIPS. High-speed extruders come with a very compact design and reach their enormous output rates with high screw speeds. The melt’s residence time inside the extruder is long enough to achieve optimal homogenization, yet short enough to prevent mechanical or thermal damage and thus ensure optimal melt attributes. In Denmark, the high-speed extruder plasticizes the material for the main layer, with in-house scrap resulting from changeovers and cuttingstamping being added to the virgin material. The material for the outer layers of the 3-layer composite is provided by two 1-75 T2.1 co-extruders. These, too, are high-speed extruders, each reaching outputs of up to 500 kg/h. “The outer layer, which comes into contact with the plant pots, is a distinctive feature of our trays. It is approved for food production as well as resistant to UV radiation and chemicals. We developed its formulation in cooperation with a Danish partner company”, the Managing Partner emphasizes.