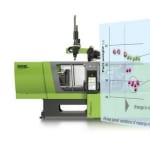
For the production of oval bowls - used, for example, for convenience meals -, the e-mac 440/180 injection moulding machine presented at the T-Plas works with Asian partners who are also well familiar with the requirements of local producers and translate these into optimally tailored solutions. The 4-cavity mould comes from CNN Plastic System, based in New Taipei City, Taiwan. The IML-automation is implemented by JET Engine Automation - also based in New Taipei City.
"The collaboration with local partners makes it possible for us to guarantee high cost-efficiency for our customers, even for very sophisticated, innovative technologies, and to also keep the delivery times for the complete production cell short," emphasises Reyre.
High productivity requires a reliable and high-performing injection moulding machine. The all-electric e-mac is exclusively equipped with especially powerful servo drives. Ejection and pressing is also handled servo-electrically. This guarantees the best possible precision and process stability while maximising the effectiveness of the machine as a whole. The highly energy-efficient machine ensures a stable production, even at continuous, round-the-clock operation
Self-optimising injection moulding machine
With the CC300 control, the e-mac provides full flexibility for the integration of robots and other peripherals, as well as the use of intelligent assistance systems from the inject 4.0 programme of ENGEL.inject 4.0 - this is the response of ENGEL to the challenges of the fourth industrial revolution, for which the name Industry 4.0 has become established. The goal is a smart factory in which production processes continuously self-optimise through the networking of production systems, the systematic use of machine, process and production data, and the utilisation of intelligent assistance systems. Producers can thus increase the productivity and quality of their production and respond very flexibly to ever more rapidly changing requirements.
ENGEL already offers an entire range of mature products for digitalisation and networking that have been proven in practice again and again, and is continuously expanding its line-up. The modularity of the inject 4.0 approach makes it especially easy for plastics processors to take advantage of the opportunities offered by Industry 4.0. Even small isolated solutions provide huge benefits.
Thanks to in-mould-labelling technology, food containers come out of the ENGEL e-mac 180 injection moulding machine ready-to-fill