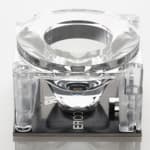
Firstly, glass is being replaced by lighter polymers that can be processed more cost effectively; and secondly, plastics offer greater scope in terms of product design. The challenge now is to strike the right balance between superior optical quality and high cost effectiveness – and this can be achieved thanks to multi-layer technology.
Manufacturing optical components in the injection moulding process entails additional challenges that cannot be resolved by standard processes in many cases: microstructures on the surface of light guide elements must be precisely moulded across the entire flow path; residual stress in moulded parts linked to manufacturing must be minimised, especially where a subsequent coating will be applied; and the optically effective surfaces on lenses with large differences in thickness must be accurately contoured.
Having taken these requirements into consideration, Engel Austria can now present its solution. Developed for the fields of mechanical and process engineering, Engel optimelt is a range of solutions aimed specifically at the production of optical components: in addition to plasticising unit components optimised for the processing of transparent polymers, the solutions incorporate various special technologies.
One of the Engel optimelt processes is multi-layer injection moulding, also known as overmoulding: This process starts with the production of a pre-moulded part which is recoated with more layers (usually of the same material) in one or more subsequent stages. The main advantage of this over the single-layer process is that the recoating covers sink marks and other defects on the surface of the previous layer, thereby ensuring high optical quality.
This benefit makes the process particularly attractive to manufacturers of thick-section components such as LED lenses. Studies on multi-layer components in the area of lighting technology have shown that boundary layers between coatings have no effect on the function of illumination optics.
Thermal simulation of the cooling process proves that the multi-layer process also offers benefits in terms of cost-effectiveness. This was demonstrated by comparing three different triple-layer variants and the conventional single-layer process in the production of a lens with a thickness of 30 mm.
In the first multi-layer variant, the three layers were applied in turn at three stations of a rotary table. For the second variant, two thick outer layers were injected into separate cavities; in a subsequent step, these layers were brought together in a single cavity and connected by means of a thin layer of plastic. For the third variant, the inner layer was produced first in an index platen mould; this was followed by two outer layers that were produced simultaneously.
To enable an objective comparison, the number of cavities was identical for each of the four processes examined. In the multi-layer variants, layer thicknesses were chosen so as to ensure the same cooling times for the individual layers in each case.
A lower mould temperature was set for the inner surfaces in each case, i.e. poorer surface quality of the pre-moulded part was deliberately accepted. This was possible because these surfaces are covered by the next layer anyway in the following step. The reduction in mould temperature was found to significantly reduce cycle times in multi-layer injection moulding.
The triple-layer process with index plate, whereby a middle layer is injected followed by two outer layers, performs best in the overall view. Since two layers are produced simultaneously in one station in this variant, the productivity of the process compared to conventional single-layer injection moulding amounts to 180 percent in the case examined. Another advantage is the fact that sink marks can be remedied on both sides.
Comparing these processes proves that high component quality and cost-effectiveness are not mutually exclusive. On the contrary: the process with the shortest cycle time actually produces the highest component quality.
Having made significant advances in multi-layer technology, Engel has applied for patents in relation to several process variants. In this way, Engel is giving its customers a competitive advantage on the promising market for plastic optical components.