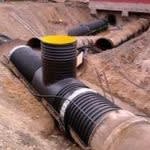
Estonian Energy, referred to locally as “Eesti Energia,” owns and operates the large production facilities at Narva, close to Estonia’s northeast border with Russia. The Narva thermal power plants have a power generating capacity in excess of 2,300MW. Estonia Energy is the leading electrical energy producer in Estonia, one of the largest providers in the Baltic region and an exporter of electricity to the Nordic power market.
Upon discovering extensive pipe corrosion in the system as part of an ongoing improvement programme at Narva, Estonia Energy turned to independent Estonia-based specialist plastic pipe producer Krah Pipes OŰ to upgrade the approximately 40-year-old steel cooling water pipes. The old pipes did not have a Borealis coating and were not made of Borealis material. Key requirements for the new network, involving two parallel pipelines running from a pumping station to the plants’ turbine room, were safety and the reduced maintenance of leak-free pipes with a minimum 30-year service life. Speed and flexibility of installation were particularly important to avoid significant power generating downtime and major cost penalties.
Borealis’ bimodal HDPE BorSafe HE3490-LS was identified as the pipe material offering the optimum balance of properties to meet the project’s criteria. The high performance PE100 material, classified MRS 10 and on the positive list of the PE100+ Association, exceeds the reference standard for the production of these pipes. It has become the reference material for many industrial pipe and pipe relining projects globally.
BorSafe HE3490-LS offers a wide range of advanced properties including low notch sensitivity. Three installation techniques - open trench, relining, and prefabricated segments for horizontal and vertical bends - were required at Narva because of the complexity of the system, which includes a 30m section beneath a concrete platform supporting 120 tonne transformers. Here electro-fusion welded pipes were pulled through and positioned in the pre-existing metal pipeline.
The consistent quality of BorSafe HE3490-LS allows for easy processing of both straight pipe sections and bends. The PE100 material creates smooth inner pipe surfaces and therefore a lower roughness coefficient than metal.
As a result, Krah Pipes was able to produce spiral wound pipes with a reduced inside diameter of 1400mm, compared to the 1580mm of the previous steel pipes whilst maintaining the same flow. A wall thickness of 20mm was used to deliver the necessary ring stiffness to ensure pipe integrity at the weld lines.
The Estonian Energy Narva plant pipe system renovation project commenced in September 2010 and was completed, system-tested and reactivated in November 2010.
“Choosing a material such as BorSafe HE3490-LS with a long track record was essential for the success of the project,” comments Peeter Kirtsi, CEO of Krah Pipes OÜ. “Also, the very good processability of the product contributed to the trouble-free production of the pipes.”
“This successful application of BorSafe HE3490-LS clearly demonstrates how Borealis’ innovation is able to bring value-added benefits to the entire chain: trouble-free production for Krah Pipes OŰ and excellent end-user performance for Estonian Energy,” adds Jane Toogood, Borealis Vice President Business Unit Pipe. “Such an example is built on our long-standing leadership and dedication to the industry.”