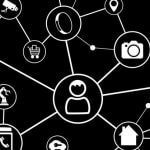
The business press frequently writes about the industrial internet of things (IoT), the fast-growing interconnectedness of the machines and systems that shape our businesses (and our lives). But the shining examples we read about tend to involve very expensive pieces of capital equipment, like combine harvesters, mining equipment and aircraft engines. So IoT may seem less relevant to the FMCG packaging line, especially for smaller companies. But it’s not.
Furthermore, this thinking can inhibit the consideration of new Lean technology, especially since plant teams may consciously avoid initiatives that involve significant IT resources, as these initiatives may be viewed as a “luxury” beyond the core mission of quality, delivery, inventory and productivity. But, it is important to recognize that advancements in technology exist today that minimize IT intensity and fit within the budgets and scope of even small FMCG companies.
I’ll get more specific about this, but first let’s examine why it matters. Take packaging equipment downtime as an example. Unplanned downtime can be very inopportune and strongly impact throughput. But a plant manager may not have the necessary data to develop insights into when or for how long unplanned downtime occurs, much less if it represents a flat or worsening trend, or if it tends to occur at similar times of day or at irregular intervals.
Without this data, it is very challenging to look for “patterns of opportunity” in identifying issues, implementing countermeasures, and boosting productivity. Simply put, many packaging operations simply lack the foundation necessary to do Lean really well. Here are three reasons why:
Getting the data is hard. Baseline data showing what is happening on the line, such as uptime and OEE data or even simple lists of downtime instances and associated fault conditions, often doesn’t exist or is of insufficient quality to spur continuous improvement. Without it, managers need to rely more on observation, feedback, and intuition, making Lean implementation effectively impossible.
Equipment and software variety. Packaging lines are often comprised of equipment from many different original equipment manufacturers (OEMs). These machines may speak different software languages, making it costly to monitor equipment using even simple Manufacturing Information Systems (MIS). This is often the root cause of challenging data collection - forcing plant teams to keep logs with clipboards and spreadsheets. While admirable and necessary, these processes tend to be highly manual making it difficult to scale and consolidate data collection and frustrating efforts to derive insights from this data.
Multiple shifts.Visibility challenges mount when plants run two and three shifts because the plant manager can’t retain direct visibility to his or her operation 24/7. In addition to the data collection issues detailed above, multiple shift operations can lead to gaps and/or inconsistencies in training processes. When a machine goes down in the middle of the night, inevitably there are fewer experts available to help problem-solve and return the line to operation.