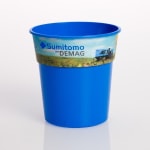
So, how can in-house or specialist moulders obtain maximum benefit from this process? How does this translate into a healthier bottom line? Sumitomo (SHI) Demag, experts in thin-wall plastics technology, offers some advice to prospective users.
Let's start by considering the disadvantages of thin wall moulding. By understanding and addressing these, the way is open to achieving and sustaining the increased levels of efficiency needed for long-term growth.
Here, judicial investment is the key. Tempting though it may be to make do with existing injection moulding plant, it can often be a case of false economy. With many contracts involving millions of mouldings, a tailor-made system can achieve the extra performance which delivers a rapid return on investment.
The first step is a thorough analysis of current and anticipated future requirements. Dave Raine, Technical Sales Manager at Sumitomo (SHI) Demag, elaborates: "It's vital to examine every potential application to ensure selection of materials, machine and tooling give the optimum blend of speed, quality and consistency. Will in-mould labelling be required? Can robotics provide a cost-effective solution to maintain increased production levels?"
The choice of machine is obviously important, and it's here that Sumitomo (SHI) Demag's expertise in hybrid - electric/hydraulic - machine technology is paying dividends for existing users and new customers alike. Designed to withstand higher stresses and speeds in a 24/7 production environment, the company's El-Exis machines have become the equipment of choice for many thin wall moulding specialists.