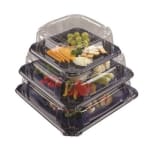
PET thermoforms in the context of the European Commission Circular Economy
"Recycling of PET thermoforms is the final stage for closing the loop of PET recycling, we have to find solutions for increasing the recycling rates, especially in the context of the new Circular Economy Package and its ambitious plastics recycling targets proposals" - this statement comes from Wim Hoenderdaal, co-chairman of the Petcore Europe PET Thermoforms Working Group, during his presentation at the Petcore Europe Conference 2016. This annual event, which took place in February this year, brought together 160 leaders and experts from the complete PET value chain to discuss the current most important topics for the industry, including the question on how the industry can improve recycling of PET thermoforms.PET Thermoforms provide many assets which make a difference. Petcore Europe is keen to demonstrate that recycling is one. Did you know that PET Thermoforms are already made of 50% recycled PET? And that PET can be recycled again?
Petcore Europe Thermoforms Working Group actively working on solutions
In order to find solutions, Petcore Europe - the European association representing the PET value chain - formed the PET Thermoforms Working Group in June 2015, comprising more than 30 companies and organisations including key players from industry and waste management. The goal is to maintain and increase the market share of PET thermoforms in the European market by improving the image of PET thermoforms as the best-in-class packaging material in this field through providing sustainable and reliable end of life solutions for PET thermoforms.More and more PET thermoformed packaging are placed on the market in Europe. Currently, the estimated demand for PET thermoforms is approximately 800.000 tons of PET resin per annum, out of which over 400.000 tons come from post-consumer recycled PET (r-PET). On average, a PET thermoform contains over 50% of r-PET. Based on their growing market share, the PET industry sees the need for an increase in the collection and recycling of these PET thermoforms.
Collection and sorting of post-consumer thermoforms need to significantly improve
The discussion starts with the heterogeneous collection situation in the EU. There is no uniform collection of trays in Europe, some countries collect all kind of plastics while others only collect PET bottles. Important steps are therefore required to improve the sorting of the incoming post-consumer packaging, for example to sort PET multilayer from monolayer trays - as PRE (Plastics Recyclers Europe) recommends – and to separate PET trays from PET bottles. The final quality of the recycled material is critical and determines in which applications it can be used: in food contact packaging, in agriculture or other markets such as strapping, polyester fibres or injection moulding applications.Concrete trials are underway in several European countries
Ongoing trials in France and Belgium are investigating what quality and percentage of PET thermoforms can be included in the PET bales without affecting the quality of the r-PET.Valorplast and Plarebel are organising such pilot scale tests in the collection and are working closely with the sorting centres to ensure the quality and composition of the bales. Sorting technologies are now allowing to take out "multilayer trays" from the "mixed PET bottle and tray stream". Thus, a stream of "PET mono-material" including bottles and thermoforms is already achieved. Further tests have to demonstrate if severe recycling conditions, high friction and high temperatures in combination with a high percentage of trays (>10%) can lead to loss of yield. When PET trays become brittle, the percentage of fines can go up.
A limited stream of bottles is currently supplied to some recyclers in France with a few percentages of PET trays in their bales. It will still take some more time to aggregate all the data and come to a conclusion on the quantity and quality of PET trays that can be included in PET bottle bales.
It is important to note that both studies are carried out with post-consumer material only, some previous work was done on post industrial waste (thermoform scrap), which is considered to be not fully representative.
Besides developing a route for the recycling of mono-material trays in combination with PET bottles, another option is to develop a route for the recycling of all PET thermoforms, mono and multi-material as well as coloured thermoforms. This might make it possible to combine these thermoforms with difficult to recycle bottles such as heavily coloured, opaque and multilayer bottles.
WRAP in the UK has launched a new project with eight companies. The objective is to recycle the complete stream of thermoforms, mono- and multi-material, into new applications. The trial will include washing, pelletizing and solid stating, and the outcome material will be available for testing in new applications.
The Petcore Europe Thermoforms Working Group has also initiated its own project, in which different partners of the supply chain work together on recycling trials. The particular aim is to determine the quality of r-PET that comes from a recycling stream mainly composed of multilayer PET thermoforms.
Design for recycling is key
The Petcore Europe Thermoforms Working Group is furthermore emphasizing the importance of design for recycling. For instance, PET trays in general have big labels and the label type is not designed for easy removal. One reason and need for using high washing temperatures and high friction is to ensure the complete removal of labels and glues. Several label producers, also members of the Working Group, are currently working on label solutions. It will be important to inform the whole supply chain to use the right label size and type.Also the use of absorption pads and the necessity to glue these to the trays is an area for further study. Alternative tray designs have demonstrated that gluing or even using these pads can be avoided. These projects and applications will be further evaluated by the Working Group.