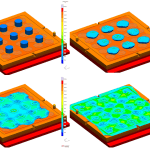
During Fakuma (12.-16. October 2021) in Friedrichshafen, Germany, Sigma Engineering GmbH presents new developments of SigmaSOFT on Booth A5-5110. The new version 5.3.1 now allows the simulation of Compression Molding processes of rubber compounds.
Up to now, simulative design of mold and process was mainly focusing on modern injection molding technology. Since SigmaSOFT is successfully introduced at many leading elastomer-molders, there was always a request to also implement the older processes, which remain technically required and/or cost-critical for manufacturing precision parts and O-rings, partly in small series. The simulation allows reliable prediction of curing degree and cycle-data. Questions around shape, weight, position and number of preforms can also be investigated. The quality of the molded parts can be optimized while reducing the material consumption, without time-consuming and costly trial-work.
„It sounds easy, but implementation was relatively complex“, explains Sigma CTO Timo Gebauer: „The challenge is, that the cavity, or the room into which we inject, constantly changes during the closing of the mold. At the same time the inserted preforms are already heating up, are plasticizing and deforming. This development would not have passed the finish line without continuous advise and validation through our customers.“
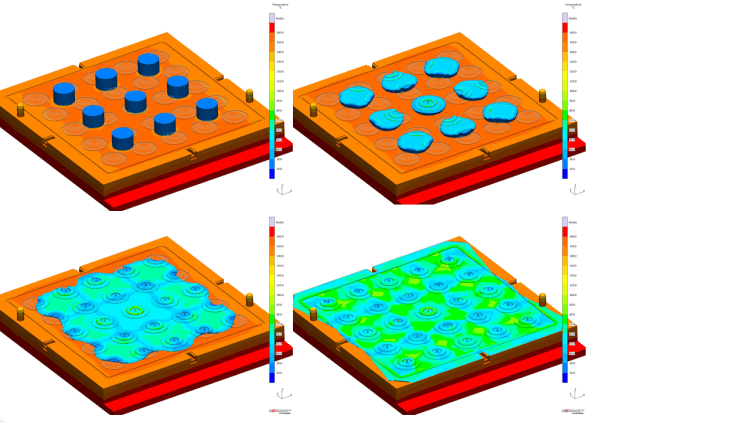
25 cavities and 9 preforms in a compression molding process
Different to Thermoplastics, in the industry only few standardized elastomer compounds are available. Therefore, SigmaSOFT features the creation of own material laws, based on internal or external measurements and supports users during implementation.
„It’s interesting, with this approach there is practically no remaining difference between Transfer and Compression Molding processes for the simulation. Technically, the injection sprue in the middle platen becomes part of the cavity. In the validation, we therefore also calculated Transfer Molding Tools successfully“, says Gebauer. „We are curious, how the most advanced simulation approach is accepted by the experienced rubber manufacturers for the oldest processes.”
SigmaSOFT v5.3.1 not only includes the first possibility to simulate Compression Molding of Elastomers, but offers especially in the area of Thermoplastics numerous innovations and improvements for example a more precise prediction of warpage and shrinkage. The Autonomous Optimization feature included in the software now also works for 2 component parts. Additionally, the material data base was enhanced.