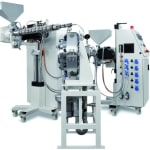
The trend towards ever more complex plastic pipes with various functional layers has continued unbroken around the globe. First, reducing material costs plays a large role in this, such as with foam core or mineral-filled pipes. On the other hand, individual layers meet technical requirements for the functionality of a pipe.
Thus, for instance, barrier layers reduce diffusion, fiber-reinforced pipes increase internal crush resistance and pipes filled with glass fiber reduce linear expansion. KraussMaffei Berstorff offers the appropriate extrusion system for every application area using specifically designed multilayer pipe heads. "We will be able to meet all inquiries for producing multilayer pipes involving up to seven layers with our pipe head product line," emphasizes Michael Hofhus, manager of the pipe extrusion product group at KraussMaffei Berstorff. "In addition to that, the wellconsidered process technology concept of this kind of complex system also plays a critical role. It ensures, for instance, that the layer thicknesses of the barrier layers can be minimized and thus the pipe manufacturer saves on costs. In addition, the market demands for flexible solutions are also met."
KraussMaffei Berstorff offers customized co-extrusion solutions that are optimally designed for manufacturing pipes with high filler content or foamed pipes. This is necessary, since the portion of filler increases continuously, which allows the processor to create a high-quality product with significantly reduced weight with enormous cost savings. "We offer our customers an intelligent machine arrangement for manufacturing multi-layered pipes with an installation area the same size as a system for manufacturing single-layer pipes," emphasizes Hofhus. "Using our co-extrusion solutions, the processor saves up to 25 percent on raw material while reducing pipe weight by up to 25 percent," continues Hofhus.
Direct extrusion systems from KraussMaffei Berstorff allow economical and cost-effective extrusion of mineral-filled pipes in a single-stage procedure. By using these systems for the production of polypropylene pipes filled with barium sulfate, for instance, individual components can be processed directly or the finished compound can be used.
A second, downstream production process can be completely eliminated. The cost savings amounts to up to 30 percent. The particular use for these kinds of pipes is as wastewater pipes in large residential buildings due to their noise-dampening properties (up to 40 percent compared to conventional pipes).
Multilayer adapters are used when manufacturing thin outer layers. These can be installed on any KraussMaffei Berstorff standard pipe head entirely without issue. Due to slight modifications of the flow contour, almost any material (including adhesive, EVOH and PP) can be shaped into a uniform layer.
Multifaceted system combinations
Furthermore, KraussMaffei Berstorff offers complex machines and systems for manufacturing pipes encapsulated with PUR, microduct pipes and interconnected PE pipes.