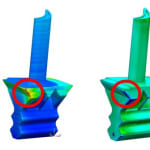
“Using the Simcenter 3D AM Process Simulation solution at toolcraft will allow us to complete our additive manufacturing workflow,” said Christoph Hauck, Managing Director, MBFZ toolcraft GmbH. “Through real-world testing, we have gained confidence that the Siemens AM Process Simulation solution will assist us in ensuring quality output from our print process.”
When metal parts are 3D printed, the method used to fuse the layers of the print typically involves heat. As the layers build up, the residual heat can cause parts to warp inside the printer, causing various problems, from structural issues within the part itself to print stoppage. Issues such as these cause many prints to fail, and make getting a “first-time-right” print very difficult. Simulation of the printing process can help to alleviate many of these problems.
Siemens’ new process simulation product is integrated into the Powder Bed Fusion Process chain in the Siemens PLM Software Additive Manufacturing portfolio and is used to predict distortion for metal printing. The product provides a guided workflow to the user that allows for the assessment of distortions, the prediction of recoater collisions, prediction of areas of overheating, and other important feedback about the print process. The AM Process Simulation solution offers the ability to iterate on a solution between the design and build tray setup steps of the workflow, and the simulation step. This closed feedback loop is possible due to the tightly integrated nature of the Siemens digital innovation platform.
The simulation data created feeds into the digital thread of information which informs each step of the printing process. This digital backbone enables the system to develop pre-compensated models and, more importantly, to feed those seamlessly back into the model design and manufacturing processes without additional data translation. This high level of integration is what customers need today in order to be successful in industrializing additive manufacturing.