The central issue is that datasheets, advice from resin suppliers, and part design criteria are all at odds at the micro scale. It is because of this that it is vital to engage with expert micro molders early in the conceptual design phase of product development, as they are best equipped to advise based on years of experience navigating material selection issues, and are best placed to indicate whether a chosen material could be an issue in part production.
Material choice is fundamentally affected by a number of important considerations. What environmental conditions will the part need to operate under? Does it need to withstand solder reflow temperatures or other high-heat situations? Does it touch the human body or other bio-materials? Are there lubricity or hydroscopic properties to include or exclude? How much should it cost?
With these questions in mind, the next step is to review some commonly used resins. It takes a huge amount of experience to select the ideal molding resin and thermoplastic for a specific application. Knowing how a given resin will perform with the desired micro-features on a part or component takes experience.
In addition to material properties, many other variables affect molded-part performance. For example, most thermoplastics come in a variety of grades that mold differently from each other, and additives such as glass, carbon, and other fibers change molded-resin properties and affect how the resin melts, flows, and fills a given geometry.
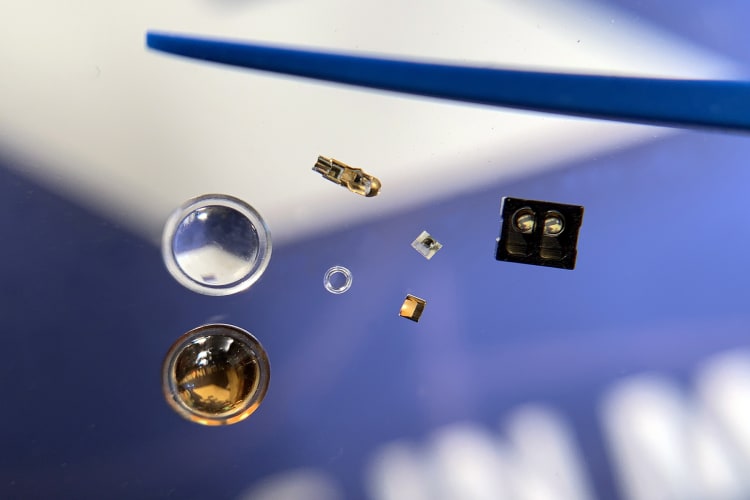
Choosing the correct micro mold material or plastics seems simple at project inception. Project leaders can simply pick the desired material that fits their project goal and inject liquid plastic into a mold. The assumption that a process for larger molds applies to micro molding, however, doesn’t play out in real-life scenarios. Thermoplastics and resins behave in unusual ways when micron or sub-micron tolerances are required.
While some projects require micro mold materials that are rigid and strong, others require resins that can maintain an ultra-thin profile. Some resins can withstand heat, while others must follow strict guidelines due to extended contact with the human body. Obviously, there are many cases where the desired material simply can’t be used due to some other design restrictions.
PEEK, for example — a popular choice in medical micro molding — is often 30% glass fiber reinforced and pelletized for injection molding, yet it cannot fill ultra-thin areas. Ultem, also an extremely popular option for micro-optics applications, also can’t fill ultra-thin micro molding projects. Consequently, to achieve OEM’s demanding project goals, balanced with various material limitations at micron sizes, the impact of material selection on DfMM should be at the forefront of everyone’s minds. The focus should be on the precise matching of chosen material to the appropriate part geometry, robustness, and performance requirements.
Summary
Micro molding projects are by their very nature complicated, and the fact that many require the repeatable attainment of extremely high tolerances demands that there is a collective focus on accuracy when looking at micro tool fabrication, molding, validation, and automation processes.
However, material selection and design for micro molding (DfMM) are also hugely important.
It is because of this that manufacturers work with micro molders as close to the beginning of the product development process as possible, as accessing expert micro molding design insight early is the key to cost-effective, timely, and right-first-time manufacturing.
Many OEMs micro molding practitioners as manufacturers. While this is in itself self-evident, they are in fact consultants. Those micro molding experts that are truly vertically integrated with all stages of the product development process under one roof have expertise in design, tooling, molding, validation, and automation. They also have the knowledge and experience to ensure that vital considerations such as material selection are given the attention that they deserve right at the beginning of the product development cycle.
Aaron Johnson, VP of Marketing and Customer Strategy, Accumold