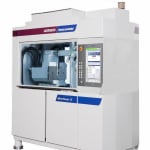
At the Compamed in Düsseldorf, the international trade fair for the medical supplies industry and medical product development, held from 18 to 21 November 2019, Wittmann Battenfeld will demonstrate its medical technology expertise with the production of a micro retaining ring for medical miniature tubes in hall 08b, booth F03-1.
The injection molding machines from Wittmann Battenfeld are already optimally suited for clean room production in their standard versions, since they are laid out for a minimal level of emissions. This applies in particular to the machines of the MicroPower series designed for the injection molding of small and micro parts. The all-electric MicroPower is designed as a self-contained cell enclosed on all sides, which simultaneously offers sufficient space for the integration of various optional pieces of equipment, such as a rotary table, robots, material dryers or temperature controllers. All drive modules of the all-electric drive system including all mechanical components are encapsulated in easy-to-clean housings.
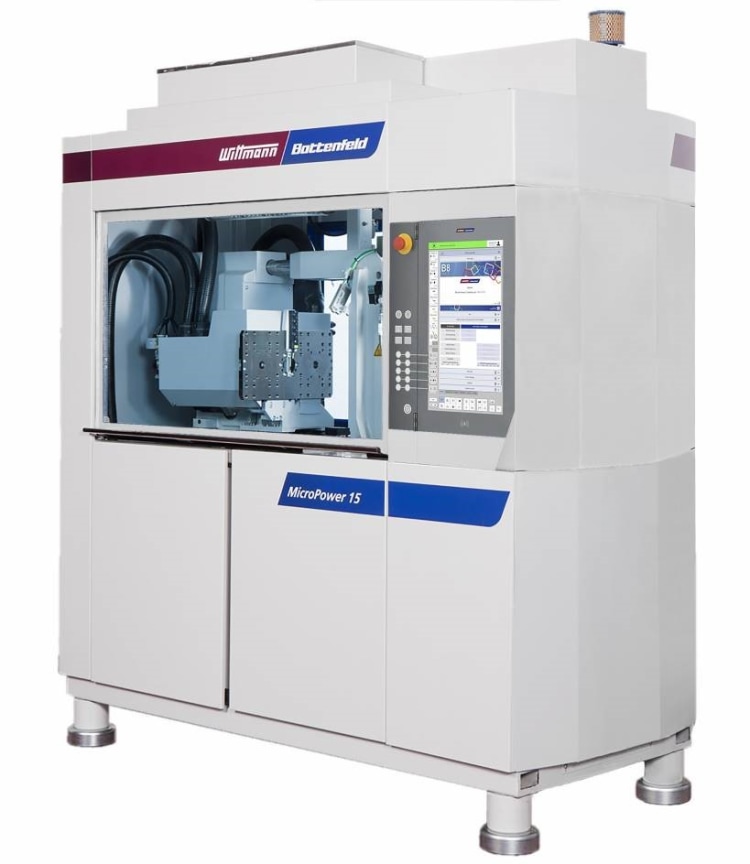
MicroPower 15/10 in clean-room version
At the Compamed in Düsseldorf, Wittmann Battenfeld will demonstrate its competence in the area of medical technology with the production of a micro retaining ring for medical miniature tubes from PC in hall 08b, booth F03-1.
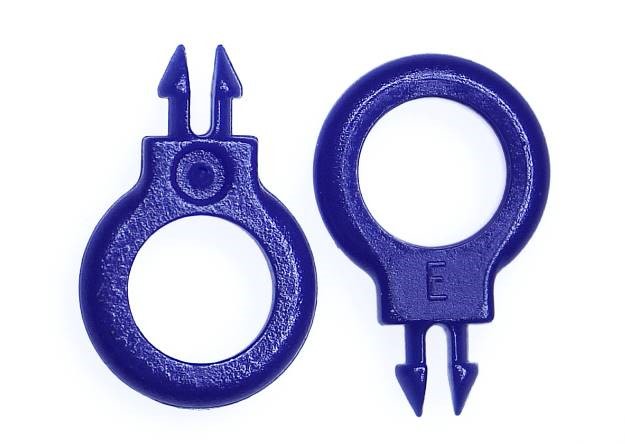
Micro retaining ring for medical miniature tubes
This micro retaining ring is produced on a MicroPower 15/10 with a clamping force of 150 kN using an 8-cavity mold from Wittner, Austria. The product has a part weight of only 2 mg. The machine comes with a rotary unit, an integrated Wittmann W8VS2 robot and a camera for complete parts inspection. Following removal and camera inspection, the parts are transferred to transport containers, separated according to individual cavities. The parts will be processed in a clean-room environment (class 6 clean air according to the ISO 14644-1 standard) which is created by using a laminar flow box inside the machine.
Source: Wittmann Battenfeld