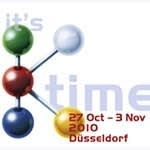
Safety and cleanliness across the board
Compared to other branches of industry, the standard of quality and documentation here is outstanding. Production to GMP (Good Manufacturing Practice) guidelines is a must. Continuous monitoring, compliance with the hygiene regulations and the full documentation of all process data over a period of years are integral to these guidelines.
The production of medical and pharmaceutical injection mouldings is closely associated with cleanroom technology. For this, the manufacturers of injection moulding machines get together with cleanroom specialists to offer a variety of cleanroom solutions tailored to the article being produced and factory conditions. A simple and inexpensive approach is the mounting of a laminar-flow unit over the clamping plates for the injection mould. The most elaborate solution involves the operation of the injection moulding machine in the cleanroom itself. The all-electric injection moulding machines now rapidly gaining ground can fully exploit their advantages here. Compared to conventional hydraulic machines, they generate barely any waste heat and, as a result of their encapsulated drive units, are free of lubricants and other abraded particles that might contaminate the injection mouldings.
Mass production with maximum precision
Single-use medical articles are items that are usually mass-produced fully automatically and to an exceptionally high standard of quality under 100% quality control. For production to be cost-effective, every tenth of a second counts. The requisite speed is provided by ever lighter and slimmer removal systems with optimised drives. An extremely fast cleanroom-compatible removal gripper was launched by Hekuma GmbH, Eching (Germany), at the end of 2009. What the supplier claims to be the fastest removal system currently available for pipette tips achieves with its linear axis acceleration rates of up to 10 g and travel speeds of up to 1,200 mm/s.
The injection moulds used for the mass production of medical technology items also of course have to be highly precise, cleanroom-compatible and at the same time economical. Along with the realisation of thin-walled products to save materials and cycle time, there is also a demand for multiple cavities and sophisticated cooling systems.
Injection mouldings in the human body
However, it is not only single-use items that originate in the injection mould. For when it comes to replacement parts for the human body, injection moulding is a preferred process. Particularly spectacular are “components” for use in the inner organs. For instance, the Moscow-based company Roscardioinvest produces a new generation of tri-leaflet heart valves from a modified polyamide. The mechanical heart valve weighing only 0.25 g proved to be a severe test for its developers. The world’s first mould for the fully automatic, finishing-free injection moulding of such heart valve leaflets has been developed and made by Köbelin Formenbau GmbH, Eichstetten (Germany).
Numerous high-precision components find their way into the human body by other avenues, among them components for use in minimally invasive surgery. Such functional parts are becoming steadily smaller, more complex and more precise – the trend towards miniaturisation in medical technology is advancing apace.
Microtechnology for the tiniest parts and structures
Microtechnology also plays a major role in diagnostics. Microstructures are required here particularly in microfluidics. A fine example is the “lab-on-a-chip”, which is a miniature analysis system with a network of intelligently interconnected microchannels. These are far less expensive to produce from plastics than from glass or silicon.
Microscopically small surface structures can be utilised in implant technology for the controlled growth of human cells. Researchers at the Fraunhofer Institute for Manufacturing Technology and Applied Materials Research (IFAM) in Bremen (Germany) focus not only on microstructured surfaces, but also on ultra-small implants. By applying micro metal injection moulding (μ-MIM), they thus produce delicate heart valve rings made of biocompatible titanium. And even replicas of the tiniest bone in the human body, the stirrup in the ear, can be produced in series as micro injection-mouldings made of titanium, biocompatible stainless steel or aluminium oxide.
These and many other examples show that injection moulding technology is playing an increasingly important role in the health sector. With innovative product developments, it has captured for itself a large market with huge growth potential. As the world’s leading trade fair for the plastics industry, K 2010 – Plastics and Rubber – will present the latest state of materials, machine and mould technology for the production of medical and medical technology plastic components. K 2010 is taking place in Düsseldorf from 27 October to 3 November 2010.