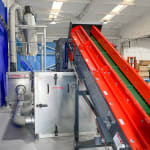
Any manufacturing and production process will no doubt produce waste in some form. So does Plastipack Limited in the UK, a producer of high-quality plastic swimming pool covers and water storage systems. By the help of a Weima two-stage reduction system, plastic scrap is recycled directly on-site - for a closed loop.
It all started with an inquiry to the British Weima dealer Fercell from Aylesford in the county of Kent. Plastipack has already had positive experience with recycling its own production waste for many years. In addition, there is an increased demand for pool foils. Consequently, the existing pelletizing system was to be renewed in order to further increase efficiency and throughput. After extensive material testing at Fercell's test center, the optimum configuration was finally worked out, with Plastipack opting for a two-stage processing solution consisting of a pre- and post-shredder including conveyor technology.
Where recycling begins: The shredding plant
Voluminous residual materials from production can be fed into the generously dimensioned hopper by forklift truck via special feed rollers. The Weima ZM 40 four-shaft shredder with a working width of approx. 760 mm first pre-shreds the film material to a homogeneous . When changing the material, a built-in mechanism helps to ensure a particularly fast screen change. The screen is guided on rollers and can be pulled out horizontally from under the shredder. In the next step, the shredded plastics are transported by a conveyor belt to the Weima WNZ 310/800 granulator, which granulates them to a of approx. 6 mm. In parallel, a drum magnet ensures that any last metal residues are safely removed.

Noise reduction during shredding and granulation
Another reason for using a shredder with four-shaft technology is its low noise level of only about 76 decibels. At around 25 rpm, the ZM shredder differs significantly from the WNZ secondary shredder, which rotates particularly fast at around 600 rpm and is correspondingly louder. To reduce the noise level of the WNZ as well, Fercell has completely enclosed the granulator in a soundproof box. It can be completely dismantled for maintenance purposes.The recycling loop is closed
Finally, the film flakes are filled into big bags by means of a suction system and packed. Plastipack achieves a throughput of around 2,500 kg per hour. The regranulate is then used again in the actual production process of pool films.
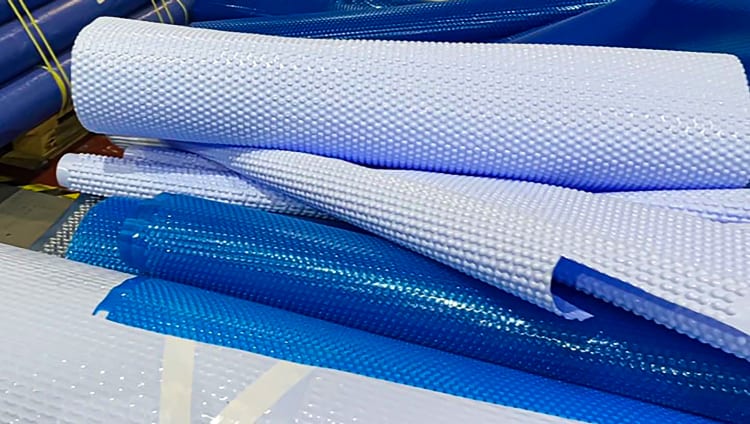