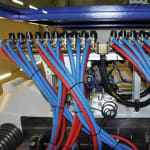
The Wittmann Wfc unit (Water Flow Control) is combining a water flow regulator and flow measurement control meeting all requirements of single mold channel control. System changes are identified through collection of theprocess data, ensuring the reproducibility. Problems like blocked channels or buckled tubes that might occur after having changed the mold, are identified immediately.
Since the Battenfeld takeover, Wittmann and Wittmann Battenfeld are constantly generating synergy through the sharing of expert knowledge that can be used for the respective development and production work. Thereby the superior target remains to meet the growing demands of the market. Wittmann and Wittmann Battenfeld are working hand in hand developing integrated solutions that are including material handling, tempering, automation, and the injection molding process itself.
It is the main target of all development efforts to always make possible the best part quality. Therefore different up-to-date techniques are used.For example the so-called online thermography method is applied, developed by the Süddeutsches Kunststoffzentrum (South German Plastics Center, SKZ) in Würzburg; or the WFC unit (Water Flow Control).
At the K Show 2010, WFC has been presented in interaction with a Wittmann Battenfeld injection molding machine to the public.The accurate mold tempering is playing a crucial role in good injection molding, and thus the tempering process is attracting more and more attention. The deformation of the part – hence the quality of the parts – is influenced by the temperature distribution within the mold. When producing complex parts, a constant tempering of the different mold segments is indispensable to get a constantly high quality.
Online thermography is identifying variations in quality – for every single shot. The technology is visualizing both overstepping and under-running of temperature control tolerances. Online thermography is a quality management procedure of parts in hot condition, in which an infrared camera makes an optical recording of the molded part, thus documenting the surface temperature (respectively the temperature distribution). Directly after the demolding the part is rotated by the robot in front of the activated camera.
Afterwards the dataset is analyzed with the aid of special software. The outcome and possible deviations from the standard are displayed on a monitor.The calculation of the deviations is done on the basis of predefined mold segments. Via an interface these deviations are communicated to the WFC. The WFC unit is executing the necessary temperature changes without any delay in real-time. The significant advantage of this technique is the external temperature measuring that is done at the molded part. Thus complex adjustments or extensions at the mold itself are not necessary.