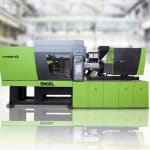
The injection moulding machine builder and automation expert will be showing three exhibits that demonstrate how to improve efficiency in injection moulding while at the same time cutting costs. The keys to success: process integration, automation and fully electric drive technology.
Competitive pressure on injection moulders in western Europe is continuing to increase", says Philippe Sterna, Managing Director of ENGEL France, "this is reflected in growing demand for highly integrated and automated system solutions, which we provide from a single source in collaboration with brand-name partners."
The best example of this is the manufacturing of complex hollow parts, which will be demonstrated live at the trade fair booth on a compact, tie-bar-less ENGEL victory 1050H/500W/200 combi machine as a 3-component application. The Multitube mould system – ENGEL's partner here is mould maker Pernoud from Oyonnax/France – supports the production of hollow components with complex geometries in a single step. This is achieved by means of a multiple stage injection process that integrates picking & placing and over-moulding in a single cycle.
Sample parts – intake manifolds for 3 cylinder engines – will be produced at the fair. For this purpose, first threaded bushings are insert-placed into the mould and then over-moulded. The pre-moulded part for injection of the second component will be turned in the mould by a Stäubli six-arm robot before the third component, a TPE seal is applied.
To support multiple component injection moulding the victory machine is equipped with a piggyback unit and a third injection unit by Babyplast. The finished component is taken off by a multiple axis robot and deposited on an integrated conveyor belt. The robot control unit is fully integrated with the CC 200 control unit of the injection moulding machine. Because the robot works inside the extended safety guarding, the production cell only needs a small footprint.
The benefit of the plant's high degree of integration is that the hollow parts are produced in a single process step that removes the need for finishing, for example, a welding process. Compared with legacy gas injection technology, the Multitube concept also ensures enhanced quality of the interior surfaces and consistent wall thicknesses.