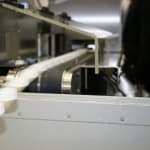
Sumitomo (SHI) Demag Plastics Machinery GmbH continues to enhance the energy credentials of its El-Exis SP range, which remain the fastest packaging injection moulding machines in the world market today.
The European packaging market is forecast to grow 1.9% annually between 2018 and 2023 . Yet, the ongoing pressure to reduce the environmental impact of single use plastic packaging up and down the supply chain, is driving brand owners, retailers, packaging converters and consumers alike to take more sustainable actions.
Consuming up to 20% less energy than its predecessors, Sumitomo (SHI) Demag is bringing two energy-enhanced El-Exis SP machines to K 2019 - a large and a small version. Catering specifically to the packaging moulding markets, the ultra-high speed range ensures manufacturers never need to compromise on quality, production efficiency or sustainability.
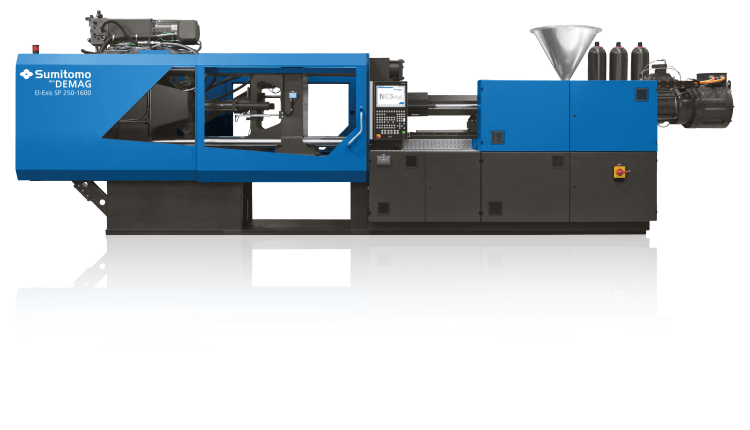
New features added to the El-Exis SP range reduces energy consumption by up to 20%
Now in its fourth generation, the El-Exis SP range is “still the fastest injection moulding machine in the world,” states Arnaud Nomblot, Director Business Development Packaging at Sumitomo (SHI) Demag. “Capable of delivering the lowest dry cycle times, the machines in the latest series have high process consistency and high energy efficiency,” explains Nomblot.
Central to the machine's fast cycle time is the hydraulic accumulator, which achieves injection speeds of up to 1000 mm/s. This enables moulders to produce even thinner packaging items. The range is also one of the fastest machines in the market for injection dynamic. “The combination of speed with high quality moulding repeatability helps to minimise packaging production waste,” adds Nomblot.
A new control valve has also been introduced to the El-Exis SP range. Regulating the hydraulic pressure during the loading of the accumulator, this new feature means the machines now consume up to 20% less energy compared to the machines’ predecessors. The amount of energy saved is dependent upon the packaging application, moulding cycle time and process parameters.
As well as being better for the environment, reducing energy consumption can significantly impact Total Cost of Ownership (TCO) and Return on Investment (ROI) for packaging moulders. Centralised monitoring of real time machine performance and energy consumption is equally critical to reducing machine downtime.
In Mould Labelling (IML), multi-component moulding for premium packaging, pails and handle assembly, along with injection compression moulding, remain part of the standard El-Exis SP offering.
Throughout K-2019, Sumitomo (SHI) Demag will run a live mass-manufacturing packaging demonstration, producing the equivalent of 130,000 water bottle caps an hour on a 72-cavity mould.
“Aimed directly at high volume manufacturers of polymer products, including caps and closures and thin wall containers and lids, the El-Exis SP range delivers greater processing control, in addition to lowering operational costs and delivering energy savings,” ends Nomblot.
The El-Exis SP is available with a clamp force range of between 150 and 800 tonnes.
Source: Sumitomo (SHI) Demag