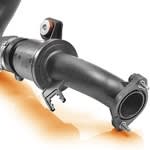
These products are a direct response to some of the main trends in the automotive industry, including weight reduction. The new materials also facilitate system cost optimizations and productivity gains, long term sustainability and reduced environmental impact.
Stanyl Diablo OCD2300 is a unique and inovative high heat PA46 material, developed specifically to meet the need for long term temperature resistance at elevated temperatures of up to 230°C. Stanyl Diablo OCD2300 joins the family of Stanyl Diablo grades that offer a key improvement in long term thermal stability. This technology, developed by DSM, extends the functional life of components well beyond the limits of other high temperature polyamides. By limiting thermal oxidative breakdown, Stanyl Diablo withstands more than 3,000 hours at aging temperatures of 230°C before its tensile strength is less than half of its initial value and short term temperatures of 260°C.
Requirements for Under the Bonnet (UTB) applications are changing constantly. Environmental requirements, EURO 5 and 6 legislation and the call for reduced fuel consumption have resulted in significant changes, e.g. the use of smaller engines with higher turbo pressures and EGR (Exhaust Gas Recirculation). As a consequence, automobile UTB components such as air ducts, air intake manifolds and charge air cooler end-caps are exposed to continuously rising operating temperatures. With increasingly critical temperature and tougher life time requirements, long term service life of components made from current thermoplastics can be at risk. Stanyl Diablo OCD2300 is currently the only high performance PA that can withstand these temperatures whilst offering better mechanical properties than other high performance polymers for these applications.
Stanyl Diablo OCD2300 was tested, validated and released by a German OEM for use in application up to 230°C CUT, where key applications include resonators, hot charge airducts and charge air cooler end-caps.
Christian Kilgus, Business Development Manager for DSM Engineering Plastics says: “Stanyl Diablo OCD2100 and OCD2300 outperform current high heat resins on high temperature stability, but also on weldability, weld strength and especially the weld’s long term heat stability. Part design and function can be reached more easily and, more importantly, UTB part reliability can be guaranteed for the lifetime required.” Stanyl materials are easy to process. During injection molding, tool temperatures of 80°C and melt temperatures around 300°C are normally used. Short cycle times can be achieved to reduce system costs.
To complete its Diablo portfolio, DSM has also introduced Akulon Diablo, a high heat PA material that bridges the gap between Akulon PA6 and PA46 Stanyl Diablo. This high performance grade of Akulon was developed specifically for use in air/fuel systems, which may be subject to temperatures of up to 210°C continuous use, and even 230°C over shorter periods.
Kurt Maschke, Global Segment Manager, Turbo Systems for DSM Engineering Plastics, says: “The addition of both Stanyl Diablo OCD2300 and Akulon Diablo significantly increases metal replacement options and meets the trend for existing plastic solutions which needs high temperature materials for new applications. Our Diablo portfolio now allows us to meet all the needs of the supply chain for Air/Fuel and Turbo applications. In addition, we also offer our standard Akulon PA6 solutions, Akulon Flex PA6 specifically tailored for flexible ducts and Arnitel TPE for clean air ducts. So we can now offer single-source solutions for all ducts, end caps and resonators. And we have extensive application knowledge to support customers with CAE, design and design optimization so they can meet OEM requirements.”
DSM has an established reputation for delivering eco-efficient automotive solutions, offering CO2/emission/fuel consumption reduction via metal-to-plastic conversion in applications such as air inlet manifolds and air ducts.