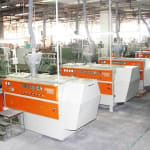
Bolta has made a name for itself extruding profile sections ranging from floor and building applications to specialized technical profile sections for the furniture industry, mechanical engineering products and for manufacturers of white goods. Bolta deploys approximately 1,000 molds to produce profile sections to its own recipes with various types of polymer from PVC to POM on 32 extrusion production lines. 150 recipes for PVC products alone make up to the repertoire of the company’s own mixing plant. This is at the heart of Bolta’s production know-how. Traditionally, with a 90% share, the manufacture of PVC products makes up the bulk of production and with it the processing of dry blend (powder) as the basic polymer. Strategically, a core component of Bolta is its own creation of polymer recipes for extrusion.
The in-company mixing plant is of great importance in terms of execution and documentation, delivering mixtures with reliable processes quickly to the production lines. The choice of color pigments for the basic polymer requires careful matching to ensure that color penetration, economic color fill and homogenization lead to optimal results in the finished profile sections.
Colors play a significant role at Bolta in marketing profile section products. Colors range from crystal clear to opaque, diffuse or solid-colored, plain and metallic colors – some 2,700 colors in total. This variety all has to be reproduced on the company’s production lines. Since the color recipes play an important role in terms of profitability and product range, the choice of the right color pigment carriers for macro-granulate, micro-granulate and liquid colors is of great importance to Bolta. In comparison to conventional master batch in granulate form, liquid colors and the new micro-batch have proven to enable much quicker color changes.
According to Stefan Beer, production manager at Bolta, speedy color changes is one of the main factors to keep production costs under control. Several mold and color changes on each production line have to be calculated in the daily schedule: “the trend towards smaller batches, short-term material planning and reductions in stock have a direct impact on manufacturing – we have to be very flexible and ensure that color changes, re-fitting and cleaning costs are kept under control”, explains Stefan Beer.
Adjustments to the recipe and degree of volumetric color fill did not result in the required effect. Lumps often formed at the front feed. What followed was a test with the Novopearls micro-granulate with satisfying results. The low melting point of 85°C and a sufficient dwell time in the screw chamber led to the required homogenization of the color pigments with the basic polymer in the melt. The degree of color fill could be significantly reduced in comparison to other pigment carriers. In addition, the spherical micro-granulate results in excellent low friction properties.
According to Stefan Beer, dosing machines for micro-granulates or liquid colors such as peristaltic pumps for liquid colors or gravimetric dosing machines in the case of micro-batches are an advantage when the materials are not pre-mixed in the mixing plant. Moreover, in the case of dual screw extruders with high thrust, the dwell time must be sufficient for homogenization.
“What matters, in particular in the case of high volume production, is to optimize the feed into the screw chamber.” For Bolta, the rheological properties of the 400µm size granulate with color pigment in a wax carrier are not only decisive factors in terms of homogenization. Shearing is also reduced by the pigment carrier. What’s more, cleaning requirements when changing colors or molds are greatly reduced. Novopearls cleans the screw constantly as the material flows through the machine.
The fact that Novopearls is dust-free is an additional positive aspect. “The cleaning effect is a striking advantage in comparison with other color pigment carriers, but above all, in comparison with macro-granulate, this helps us to lower mold changing times. When we can halve the time for a color change, this helps us cut costs,” says Stefan Beer.