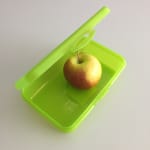
Windsor/Hanau represents the servo-hydraulic toggle injection moulding machine range of the Taiwanese FCS Group in Europe. During K 2019 these partners will present the latest engineering result of FCS to the market in hall 12, stand B11 - a servo-hydraulic injection moulding machine, type FCS FA-160, with 1600 kN clamping force and some features, which give new impetus to the topic of productivity. In addition, plastics experts will learn at the "PxP InfoPoint" how they can upgrade a single-component IMM to a multi-component system without great effort.
Windsor and Fu Chun Shin Group, Taiwan (FCS) have been working together since 2016: FCS develops and builds injection moulding machines (IMM for short) for the European market according to Windsor standards and specifications. System supplier Windsor, Hanau/Germany, is responsible for the marketing, installation, spare parts supply and service of these machines, with clamping forces from 300 to 37,000 kN, in all EU and EFTA countries. After all, the Hanau-based company has over 65 years of expertise in injection moulding technology and a correspondingly well-developed sales and service network. Peter Kochs, Managing Director at Windsor: "The partnership with FCS works perfectly, as does the technology of the machines which correspond to the regulations of industry 4.0 and IoT. In terms of technology and price-performance relationship, they are in excellent competition with comparable European products. After all, Windsor is responsible for this".
The new FA system from FCS
At the stand B11 in hall 12 the newly developed FCS FA-160, a servo-hydraulic toggle IMM - 1600kN clamping force - works with a robot system from WEMO. In no time at all, the robot demoulds the polypropylene products - snack boxes (see picture) from Miraplast, Austria, measuring 190 x 128 x 50 mm (l x w x h) or 82 grams in weight - and places them on the conveyor belt moving towards the visitors. The FA version is the successor to the SD series in the clamping force range between 500 and 3700 kilonewtons. The new series has already proven itself in the packaging market, in the building industry (fittings), in the IT sector (small appliance housings), in the household goods industry and in the automotive sector. It is available for this purpose with newly developed high-performance screw cylinders, a special linear guide for the injection unit and an effective servo injection system operating in a closed control loop. Some technical data: theoretical shot volume = 393 cm³, shot weight in PS = 357 gr, injection pressure = 1539 kgf/cm², injection speed = 120 mm/sec, mould size = 310 x 310 mm, tie-bar distance = 470 x 470 mm, movable platen = 705 x 705 mm, machine dimensions (l x w x h) = 5510 x 1560 x 1840 mm, machine weight = 5650 kg.
In general, FCS has designed the fixed platen of the FA series more strongly - in favour of the service life of the moulds. The moving platen has been optimized for the same purpose. The clamping force acts optimally through the centre of the platen. In order to offer more flexibility for the use of special moulds, the distances between the tie bars have been increased. The precision-controlled closing and opening speeds and a multitude of other process and product parameters are displayed, monitored, optimized and logged on the new FCS 6500 12" MMI touchscreen (man-machine interface) and communicated with higher-level production control systems of the factory management. "We at FCS only offer servo-hydraulic machines because they represent the latest high-end technology in this segment. The machines are as good as European machines in terms of quality. The price/performance ratio of the FCS machines is second to none", underlines Peter Kochs, Managing Director at Windsor. A fully electric CT-e 300 injection moulding machine with a 4 + 4 stack mould for an IML application (in-mould labelling) will also be in operation at the FCS stand.
PxP InfoPoint
The PlugXPress series - PxP from 42 to PxP 1780 - corresponds to an injection moulding machine without clamping unit. This Plug & Play supplementary injection unit can be connected to any IMM. "The unit is a mobile injection moulding machine without a clamping system, which can easily be attached to any IMM without high assembly costs. It injects the second and/or several subsequent components into the mould", explains Andreas Janisch, Product Manager at Windsor. The PxP unit - essentially consisting of a three-zone screw cylinder unit (16 to 105 mm), a B&R control system and a 15" touch screen - communicates with the IMM via an interface. As a result, the customer does not have to change his existing system. "All process steps are easy to perform - this simplifies the tasks at the IMM enormously," explains Andreas Janisch. Now a technical upgrade is also being tested so that the B&R control system can operate via "Open Protocol".
Furthermore, Windsor represents the sales and service interests of Japan Steel Works, LTD. for injection moulding machines (IMM for short) on the German market. In Hall 13, Stand B 45, trade visitors can see for themselves the performance capabilities of two fully electric IMM. The J 100 ADS (1000 kN clamping force) produces sample parts using the special SOFIT foaming process and the all-electric FLIP additional injection unit. The J 350 ADS (3500 kN clamping force) is in action processing biodegradable plastics. The machine works with new servo drives - developed in-house by JSW. The JSW booth will also feature a blow molding machine with TA-HARA technology and a compounding extruder of the TEX-αIII series for laboratory applications.
Source: Windsor