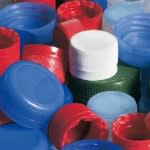
Motivated by a need to bring cap manufacturing under internal control – to set up personalised solutions that meet their specific manufacturing requirements – the German company soon identified the Sacmi's complete line as the perfect tool with which to achieve its goals.
The five installed lines manufacture caps with a diameter of 28 mm (standard 1881) and a weight of about 2 grams, with per-line output rates of approximately 1,500 pcs/min. Successful testing of the first production line showed that Made-in-Sacmi compression technology provided the ideal solution in terms of both competitiveness and cost-benefit ratios: Vitaqua's technical staff were so impressed that they quickly confirmed the purchase of further 4 manufacturing lines.
Most significantly, as Mr. Reinhold Juelg, R&D Manager at Vitaqua, points out, "the advantages associated with this technology, compared to injection, allow us to work at lower extrusion temperatures with significant energy savings". For Vitaqua, that advantage is enhanced by the fact that water cooling flow rate temperature is in the range of 20-25 °C, meaning, according to Juelg words, that “the water in the circuit only needs cooling in the summer months”.
In the opinion of the German technicians it's also - and above all - the dimensional repeatability of the cap that makes the difference. "Sacmi technology", highlights the Vitaqua R&D manager, "used in conjunction with the correct masterbatch, minimises waste and gives the line excellent overall efficiency: on the basis of random testing effected on a 10-hour production run, 900.000 caps were produced and only 35 faulty ones rejected. Average cap weight is remarkably consistent. In the bottling line, since the caps production equipment has gone online, the percentage of bottles with caps incorrectly applied due to dimensional variations has dropped from up to 0.5% to below 0.02%. That was one of the decisive criteria."
Thanks also to the customer's faith in the project, great results have been achieved in terms of feedback and availability: since the installation of the caps production lines the number of complaints received from all the three German plants belonging to the Beverage Group since start-up in march 2013 till today was reduced to zero.
Last but not least, the enhanced output flexibility provided by Sacmi technology, with colour change time in less than 10 minutes and minimisation of associated waste material, meets another key need: solutions flexibility - shared by all the world's major bottling players.