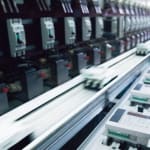
Manufacturing industry is currently undergoing a period of rapid change. In concrete terms this can be seen as the move from automated production to fully digitised manufacturing. New goals are continually being set, but the target is to use existing standards to achieve them.
The way things will develop depends largely on the requirements of end users, which have changed massively in recent years. End users increasingly expect more product variety and customisation, but at a similar price point.
An obvious example is the speed at which online configurators have influenced the car market. Vehicle manufacturers have long relied on options lists to make a profit from selling a passenger car. However, competition has increased and more technology has now become standard. That has resulted in the requirement for a larger range of personalisation options to be offered in order to entice buyers into choosing a certain model. For less complex end products, the customisation-on-demand process can happen even faster.
With the rise of online ordering, the link from a sale to a machine tool or a robot altering its work pattern is closer than ever. To satisfy this demand suppliers require the highest levels of flexibility from their manufacturers throughout the supply chain. They have to react very quickly, changing production numbers for individual items on the fly. This is where the 'smart factory' starts to come into being.
As an automation solutions provider, Mitsubishi Electric is a partner to industry. We support our customers in the development of their business ventures with consultation on industrial automation and Information technology.
All our activities relating to the digital transformation of enterprises - creating the 'smart factory' - are part of our e-F@ctory' concept. This encompasses the e-F@ctory Alliance, a worldwide active network of cooperating companies.
The network brings together manufacturers of industrial components as well as specialist system integrators and software providers. These partner companies collaborate at an individual level to offer flexible, optimised solutions.
A great example of the e-F@ctory Alliance working toward delivering proven solutions to Industry 4.0 challenges can be found at Mitsubishi HiTec Paper Europe GmbH in Bielefeld, Germany. There, a more holistic approach to predictive maintenance has been achieved by implementing a Smart Condition Monitoring solution developed in cooperation with FAG Schaeffler.
The technology allows a whole range of parameters from the coating machine and its ancillary parts to be monitored around the clock. That data is then used to analyse the condition of individual components as well as the health of the individual machine and of the wider plant. The information gained from the system includes maintenance recommendations. This enables intelligent decisions to be made in advance, based on real need, not simply routine.
The solution has created a new working methodology, drastically reducing unplanned downtime and the risk of subsequent damage. Overall, the result is vastly improved predictive maintenance, optimised asset lifecycle management and production, while reducing total operating costs.