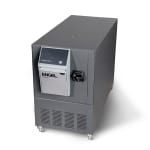
At K 2019, which takes place in Dusseldorf from October 16 to 23, Engel is expanding its range of e-temp temperature control units with an XL variant. With this new variant, the provider of integrated system solutions for injection moulding is reacting to its customers' requirements. In many applications the new development reduces the footprint required for mould temperature control, thereby simultaneously improving efficiency.
The new and larger variant has been upgraded with a higher pump capacity. This now makes it possible for one temperature control unit to replace several smaller temperature control units that operate at the same temperature. The footprint is thereby effectively reduced. At the same time, the piping requirements, energy consumption and investment and maintenance costs are also all reduced.
In addition to pump capacity, the maximum available heat output has increased. With the XL variant this is optionally 16 or 32 kW. The smaller e temp models achieve heat outputs of 8 or 16 kW.
Even in the new size, e-temp retains the compact dimensions and fits beneath the clamping unit of many injection moulding machines. It therefore requires no additional footprint.
Temperature control unit and injection moulding machine are fully integrated
The e-temp temperature control units that Engel has developed in collaboration with HB-Therm play a central role in Engel's integrated mould temperature control solution. With the iQ flow control software, the temperature control unit and CC300 injection moulding machine control merge into a single unit. The whole process is displayed on the injection moulding machine's operating panel. The iQ flow control software regulates the volume flow rate and dynamically and automatically adjusts the temperature control process to match the respective process conditions. To achieve this, the software uses the measured values determined by the e-flomo electronic temperature control water manifold which is installed in the injection moulding machine. This results in constant temperature control conditions and significantly improved energy efficiency thanks to the automatic demand-based control of the pump RPM of the e-temp temperature control unit.