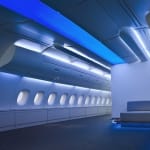
The total cost of the project "Manufacturing processes for products made of composites or engineered metallic materials" amounted to almost €5 million and EU funding amounted to €3.6 million. The project was coordinated by the VTTT Technical Research Centre of Finland.
"Essentially, we helped develop and manufacture lightweight, sustainable and durable composite sandwich structures for a range of different applications," explains Lisa Wikström, INCOM project coordinator. "The key to our success was the use of new ways for manufacturing cellulosic nanofibre, or CNF, a nano-scale material derived from cellulose found in biomass and bio-waste, which is used to reinforce the composite sandwich structures."
Lightweight sandwich core structures create new opportunities for decreasing the weight of composite structures and/or replacing petroleum-based raw materials in composites. For example, sandwich composite materials can replace monolithic structures in many applications, thus saving input materials, reducing the overall weight and generating less waste at the product’s end of life. Sandwich structures with low cost core and increased performance skin materials yield lightweight and cost-effective composites. Moreover, the reduced use of materials in sandwich composites, compared to monolithic structures, reduces their environmental impact. In transportation and aviation, lightweight structural materials mean fuel savings and a reduction of CO2 emissions
Manufacturing CNF
Specifically, the project developed a range of products, including: rigid nanocellulose fibre-biopolyurethane composite foams, extruded and particle foamed bio-based polylactide foams, cellulose fibre reinforced honeycomb structures, and polycarbonate honeycombs with outstanding fire-smoke-toxicity performance. To do so, the project used two approaches for manufacturing, modifying and processing CNF. The first involved the fibrillation of cellulose in a pre-polymer using basket bead milling. The second involved fibrillation of bioresidue-based cellulose in aqueous media by grinding and developing a quality assessment tool for optimising the process.Pilots implementing both CNF production routes were then performed with various industrial partners. CNF reinforced resins were used to manufacture composite and lightweight sandwich structures, for which three types of cores were developed: expanded NFC reinforced bio-based PU foam, bio-based thermoplastic foam, and thermoplastic honeycomb. Furthermore, industrially viable production methods were also developed.
"CNF reinforced bio-PU foams were found to perform at the same level as commercial PU foams," says Wikström. "We also found that the addition of CNFs further improved the compressive strength and modulus of the foams."
Potential for a big impact
The project led to the development and upscaling of a number of novel composite structures and viable processing techniques, each presenting a high potential for commercialisation. Furthermore, these solutions have led to new and improved production methods and sustainable and/or cost-efficient product demonstrations, which will likely lead to new commercial products and product families."With the results of achieved by the INCOM project, the composite industry now has better possibilities for production using enhanced, more environmentally friendly and less hazardous processes and materials, resulting in products with reduced weight, optimised performance and improved end-of-life disposal," adds Wikström. "The combination of new manufacturing processes with new materials and surface treatment concepts promotes new design and creates employment opportunities, particularly for product development and engineering in Europe."
Source: European Commission
Photo: Diehl