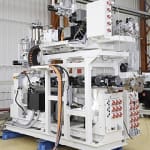
The soaring cost of energy poses problems not only for private households, but increasingly also for industry. Manufacturing industries are facing escalating costs, driven largely by the rising price of power. In the past eight years, prices for industrial electricity in Germany have increased by as much as 120%. More and more companies are finding that cutting power consumption is a fast and effective way of reducing costs. In the plastics processing industry, energy consultants can advise on energy saving measures; the consumption of every machine needs to be scrutinized.
As a leading supplier of extrusion machinery, KraussMaffei Berstorff has taken up the power-saving challenge. The starting point is always a detailed energy audit of the main energy consumers in an extruder in order to pinpoint the modules with the highest energy consumption and the greatest losses. The main areas of heat loss are the barrel of the plasticizing unit and the drive train - the gearbox and a conventional DC motor. In response to these results, KraussMaffei Berstorff offers solutions that address these heat losses.
Low maintenance and cleaning effort improves uptime. This in turn improves extruder productivity. A reduction in the number of wear parts, eg, no carbon brushes or collectors, makes the machines even more rugged and reliable. The AC motors also show substantially better behaviour under part-load than the DC drives.
One of the contributory factors here is the sharply reduced reactive current requirement. KraussMaffei Berstorff also offers the water-cooled AC drives as an option for production under cleanroom conditions. With this new energy-saving measure for the 36D Exclusive single-screw extruder series, KraussMaffei Berstorff is helping its customers to save energy and costs in manufacturing. The result is cost-competitive and environmentally-compatible production.