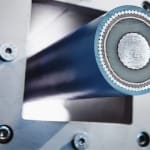
As an alternative, a High Performance Thermoplastic Elastomer (HPTE), based on Polypropylene, can be used as insulation material during manufacture of medium and high-voltage cables. The material shows good electrical and thermo-mechanical properties, comparable to those of XLPE and in some aspects even superior. The HPTE does not require a cross-linking and no degassing treatments. This means that the complete cable is manufactured in one production process without a CV line and could be jacketed directly in the inline process.
No matter which approach is applied respectively, which material is used, the purity of the insulation material is an essential criterion for the durability of the cable or by implication for the risk of a breakdown and the accompanying costs. At this point, the advanced purity inspection and sorting system PURITY SCANNER comes into focus.
Today, inspection systems are used either in laboratories or for online monitoring during the production process. The majority of these systems are based on optical technologies to detect contamination on the pellet surface. Contamination inside the pellets cannot be detected by using this method. The inspection and sorting system PURITY SCANNER allows for a 100 % online quality assurance. By using X-ray technology and optical technology, contamination are reliably identified on and inside the pellet and automatically separated.
In addition to online inspection and sorting devices, the PURITY CONCEPT Systems are available for on- and offline inspection and analysis of pellets, flakes and tapes/films. The models of the PURITY CONCEPT Systems are designed for smaller throughputs as well as production lines where sample testing is sufficient, or the control of incoming goods is required. Depending on application, the systems are equipped with X-ray technology (X), Infrared technology (IR) or optical sensors (V) and are used for the detection of contamination in XLPE and HPTE material.
An example: The laboratory inspection and analysis device PURITY CONCEPT X with X-ray technology inspects up to 3,000 pellets (200 ml) that are placed on a tray. Within seconds, these pellets are inspected for contamination. Subsequently, contaminated pellets are optically highlighted. Quality assurance does not get better than this.
For comprehensive process optimization, cable manufacturers combine the online inspection and sorting system PURITY SCANNER with an offline inspection and analysis device of the PURITY CONCEPT Systems.
The PURITY CONCEPT System detects and highlights the single contamination from the 200 ml rejected material. This interaction of online and offline inspection and analysis ensures the monitoring of material purity as well as the creation of a database to avoid contamination in the future.