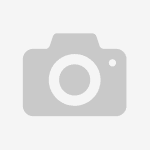
This material has gone into its first serial application at Bosch, for a fuel filter housing for the Audi A4 and A5. The new type of plastic is available in commercial quantities on a worldwide basis.
For quite some time now, the pump and supply units of fuel supply modules have been made of POM such as unreinforced Ultraform S2320 003 or glassfiber-reinforced Ultraform N2200 G43. For its filter unit, however, Bosch demands compliance with the high requirements of SAE standard J1645 (version of August 2006), which can only be met by a conductive material.
This standard of the Society of Automotive Engineers (SAE) recommends a maximum specific volume resistance of 106 ohm.cm for materials that will be used in components through which fuel flows. Under measuring conditions according to ISO 3915 (four-point method), the conductive Ultraform attains a value of a mere 30 ohm.cm, making it 30,000 times more conductive than necessary, so that it meets the requirements of SAE J1645 with ease. This eliminates the risk of electrostatic charging and sparking as fuel flows through the filter.
Thanks to the type of additives and the way they have been incorporated, the new Ultraform has retained its POM-typical properties such as toughness, dimensional stability and elastic resilience. Moreover, when this material comes into contact with fuels, it is stronger and more creep-resistant than conventional POM, in addition to which it is less costly than other conductive plastics.
Thanks to its abrasion resistance, it is just right for the manufacturing processes employed for (micro-)electronic components where, under clean-room conditions, static charging has to be prevented and the absence of dust is paramount.
This material is easily processed by laser welding and injection molding. The carbon nano tubes are firmly fixed in the plastic matrix and the material can be handled safely throughout its lifetime. BASF developed Ultraform N2320 C and optimized it for this application in a collaborative effort with Bosch. Various application-technology tools from BASF’s laboratory played a role in designing the component: parts calculation using the CAE instrument ULTRASIM, welding and burst-pressure experiments as well as creep-resistance tests. The fuel filter housing is produced in Budweis in the Czech Republic. Bosch is planning to use the new Ultraform globally.