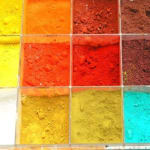
Brand owners and packaging producers trying to reach sustainability goals profitably are expressing keen interest in the newest color and additive technologies for plastics that are now available from Clariant Masterbatches.
It is clear that customers want help in implementing a more sustainable business model. So Clariant has made it a priority to develop solutions involving recycled, renewable and biodegradable materials, as well as technologies to help reduce material use and energy consumption.
“Major consumer brand companies are aggressively seeking ways to improve the environmental profile of plastics packaging,” observes Alessandra Funcia, Global Head of Segment Packaging for Clariant, “especially if they can do so while maintaining profitability. We try to work with our customers and show them several different ways to realize their objectives and we always provide a complete business case analysis for the total package, including materials, manufacturing efficiency, productivity, etc.”
In conventional materials or in biopolymers, foaming has the potential to yield many environmental benefits including reducing overall resin usage and weight – in some cases by up to 30% – often with no loss of physical properties, mechanical performance or appearance, even in challenging applications. For instance, when black, navy and other darker colors are used in injection-molded polypropylene, the newest Hydrocerol chemical foaming agents plus Clariant-optimized molding conditions make it possible to achieve a smooth, glossy surface finish. This is an important improvement over the matte finishes and frosted looks that compromised critical appearance parts.
Material savings is not the only benefit. Lighter weight packaging is easier to transport so shipping costs and fuel consumption can be reduced. In processing, Hydrocerol reduces the melt viscosity of the base resin, allowing for faster extrusion rates and reduced cooling time, both of which contribute to shorter cycle times and, ultimately, lower energy costs and higher productivity.
Most of these Clariant products can be supplied in traditional solid masterbatch form or using new liquid vehicle technology (LVT), which can offer significant sustainability and economic advantages in many applications. Liquid masterbatches disperse readily through the polymer matrix so, in some colors, the amount of colorant needed to achieve the desired look can be cut by 50% or more.
This is especially true for translucent or transparent colors in clear polymers like PET, polyethylene and polypropylene. Liquids can be metered very precisely, eliminating the risk to over-saturating the color. When it comes time to change from one liquid color to another or from liquid color to solid, the switch can be made in a fraction of the time it takes to purge solid color from the processing machine so less scrap is generated. Liquid masterbatches can also be formulated so that they actually improve the flow of the polymer, resulting in faster fill times and shorter injection molding cycles, as well as improved extrusion throughput or lower required screw speeds.