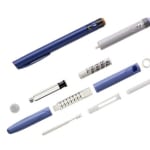
The Mevopur brand covers a wide range of products - including color and additive concentrates (masterbatches), and finished plastic compounds - uses ingredients that have been biologically evaluated to ISO10993 and USP <87>, <88> Class VI.
"The way in which pharmaceuticals are packaged and used by patients is changing rapidly," explains Steve Duckworth, Clariant's Global Head, Healthcare Polymer Solutions, "and color has an important role to play. Not only does color help identify products, it also can make delivery devices more attractive and, thus, may help to increase the likelihood that patients will adhere to their treatment regimen."
However, he continues, "color also can introduce processing variability." Pigments have an influence on how polymers, particularly those made of crystalline polymers such as polypropylene (PP), acetal (POM), may shrink as they cool and solidify. Differential shrinkage can mean components don’t have sufficient clearance to function as designed. This phenomenon may only become apparent during storage stability testing, or when an existing device is converted to a different color (e.g. for a different brand). Also, in caps or closures used in pharmaceutical packaging, these color-induced variations can result in changes in ovality or leakage.
Some manufacturers may see no alternative solution except for an expensive tooling redesign, resulting in delayed product launch and/or expensive re-validation. However, this need not be the case, as a leading producer of auto-injector devices recently discovered with Clariant's assistance.
The company wanted to market a range of colored devices to match the requests of different customers, but they had encountered assembly problems due of variation in dimensions, and they were faced with a delay in production. With its longstanding expertise in polymer color and additive technology, combined with its dedicated healthcare-market team, Clariant recognized the problem and was able to measure the influence how different pigments influenced crystallization of the PP polymer chosen for the outer body. Clariant proposed to combine Mevopur colors with a Mevopur nucleating additive, which would eliminate the difference in crystallization and yield components with consistent dimensions regardless of color. The optimized formula was developed into both a 'ready- to-use' Mevopur compound and a 'combibatch' concentrate to fit with the customer's different processing needs.
"Although the use of nucleating additives is not new," Duckworth concludes, "the fact that the additive is available as a Mevopur product gives the customer a level of regulatory support and change control that is not normally available but increasingly essential for materials used in many medical devices and pharmaceutical packaging products. The combination of Clariant technical expertise and focus on the needs of the market allows us to help the healthcare sector realize the same creative opportunities that are available in the less-regulated personal-care-packaging and consumer-goods markets."
Mevopur 'Controlled, Consistent, Compliant' products are developed and manufactured at three 'GMP ISO 13485' certified and dedicated production facilities located in USA, Europe and Asia.