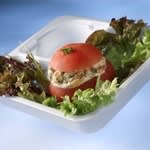
Daploy HMS PP is unique in offering the highest melt strength in combination with highest melt extensibility. This combination is required in order to allow bubble formation and growth during the foaming process without collapsing. It creates a closed cell structure without failures which ensures a smooth finished surface for the final product. These are important criteria for achieving consistent, high quality, low density foams between 40 – 200kg/m3 - as well as superior packaging aesthetics. As a result, Daploy HMS PP allows the converters to enter new application opportunities by extending performance, processing and environmental benefits of PP low density foams for food and consumer packaging.
Daploy HMS PP has a wide mechanical property range, including good rigidity and cushioning performance. The materials offer high heat stability and can adapt easily from cold to hot environments, making them particularly well-suited for lightweight thermo insulated food packaging such as refrigerated microwaveable ready meal trays and cups for hot soup and beverages. Additional applications include foam trays for fresh meat and fruit packaging as well as cap liners for food and consumer packaging.
Good chemical and high thermal resistance add to the material’s ability to give high performance to technical foams for door liners, engine shields, trunk liners, air ducts and other automotive and non automotive technical applications. In addition, HMS PP is used as processing modifier in PP blown film and blow moulding processes as well as for extrusion coating processes.
Low density foams based on Daploy HMS PP make a significant contribution towards material savings and therefore weight reduction and lower material usage compared to high density foams or other non-foamed application alternatives. This enhances both environmental credentials and cost-efficiency advantages for the manufacturer.
Daploy HMS PP materials are non-cross linked, allowing them to be remolten
and recycled. As a mono-material solution, Daploy HMS PP provides straight-forward recycling compared to multi-material or cross linked solutions. The use of a recyclable, single material solution for an application aids sustainability by the manufacturer.
“The unique property combination of highest melt strength and highest extensibility offered by Daploy HMS PP extends the benefits of PP to the manufacturing of high performance low density foams,” comments Wim Roels, Senior Vice President of Borealis’ Film & Fibre Business Unit. “This delivers a valuable material alternative with important performance and productivity-related advantages which can be easily recycled and opens up the potential for new application opportunities for our customers in the packaging and automotive sectors. We are pleased to showcase this advanced product range as part of our Creating New Horizons theme at K 2010.”