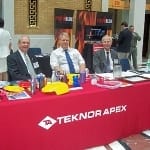
The high speed extrusion line ran a 0.105 in. (2.67mm) OD x 0.020 in. (0.508mm) wall tube up to 830 ft/min (253 m/min.) line speed. At 600 ft/min (183 ft/min) line speed, tight tolerances of +/- 0.0004 in. on the OD and +/- 0.0001 in. on the wall thickness were held.
The extrusion system consisted of an American Kuhne ULTRA series 2.0 in. (50 mm) extruder with AKcess Level II Touchscreen System; inline spiral flow die head; Conair multi-pass vacuum tank with servo driven wheel to minimize the rubber band effect and to minimize tension within the process; servo driven nip roller puller; automatic cut and transfer coiler and a Zumbach ID/OD/WALL tube measurement system with closed-loop control of the OD and wall thickness. The compound used in this run was MD-585, an 83 Shore A compound that is part of the Medalist MD-500 series for tubing applications.
“American Kuhne is a premiere supplier of extrusion systems and has great expertise in the technology for producing medical tubing,” noted Nick Sandland, senior medical marketing manager for the Thermoplastic Elastomer Division of Teknor Apex. “The company’s flawless high-speed demonstration run of our Medalist elastomer adds new confirmation that MD-500 series tubing compounds truly are fully practical alternatives to PVC.”
Recent innovations in radio frequency welding, adhesive bonding, and solvent bonding enable components produced from Medalist elastomers to be used as readily as PVC in the assembly of medical devices, Sandland noted. “Today it’s clear that Medalist MD-500 compounds provide the total package of requirements for successful tubing applications - processability, ease of fabrication, and outstanding end-use performance.”
The American Kuhne Spring Medical Seminar and Open House offered participants valuable technical knowledge and processing tips about medical extrusion. The sold-out two-day event attracted over 80 participants.
The key message delivered for Teknor Apex at the event was that the Medalist MD-500 Series compounds are the first fully practical alternative to PVC for many tubing applications, noted Sandland. “It’s not just that they provide mechanical properties equal to or better than those of the flexible PVC widely used for medical tubing; at least as important, they yield tubing that looks and handles like PVC. This means similar crystal clarity, clamp resilience, resistance to kinking and necking, and an overall PVC-like ‘feel’.
Sandland also cited some important advantages over PVC: “Medalist elastomers are substantially more flexible. They are less dense, meaning that one can process more feet of tubing per pound of compound. And they exhibit minimal color shift upon heat aging after exposure to gamma irradiation, the most severe type of sterilization.”
A typical compound in the series, Medalist MD-575, actually exhibits 70% less heat-aged color shift than a gamma-stabilized PVC compound of comparable hardness.
“The Medalist material was easy to handle while stringing up the line and also while coiling at the end of the line,” said Steve Maxson, VP Extrusion Systems of American Kuhne. “The material is extremely forgiving, with very stable processing conditions at high extruder output levels, which means that tight tolerance levels can be achieved at very high production line speeds.”