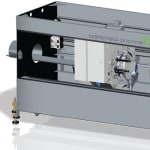
With the helix-63-5 VSI pipe die, battenfeld-cincinnati is adding a new pipe die size to its extensive product range. Now that 5-layer pipes with a layer of EVOH serving as an oxygen barrier and diameters of up to 32 mm have been established for some time in floor heating systems, the market now also requires these functional pipes in larger sizes. These are ideally suited as inlet and supply pipes in floor heating systems, or for laying in contaminated soil. Therefore the machine manufacturer now offers the new 5-layer pipe die for making pipes up to 63 mm in diameter and plans to add another new die to its portfolio in the near future as well, to accommodate pipe diameters of up to 125 mm. In the production of 5-layer pipes with an oxygen barrier, EVOH processing constitutes a special challenge. This is why, in designing this die, battenfeld-cincinnati has paid special attention to a short dwell time of the EVOH inside the die and optimal distribution of thin layers with extremely narrow tolerances.
The helix-63-5 VSI die is based on a classic VSI die with the well-known two-step distribution concept consisting of a spiral mandrel distributor and a lattice basket. This structure ensures best possible distribution, homogenization and throughput with minimal pressure build-up. For the subsequent coex layers, a double mandrel is used as the basic distribution element, followed by either a spiral mandrel or a lattice basket, depending on the material. The modular design of the die facilitates its conversion for the production of 3-layer pipes, as well as disassembly for thorough cleaning. Minimal melt dwell times ensure short color changeover times. Finally, a choke for the two adhesive layers is responsible for regulating their flow rates from only one extruder.