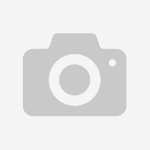
In every manufacturing industry, improving quality and reducing wastage is of prime importance. None more so than in plastic bag manufacture, where the Series 1000 Web Cleaner from Meech International is successfully used around the world to remove waste particles, or chad, after the die cutting process.
When manufacturing plastic bags, the film is printed and then goes through a die cutting process to either add ventilation holes or to punch a Euroslot. After die cutting, the film is then rewound and sent on to customers to be used to wrap items before being sent to the stores or to be used directly by the shopper.
Most die cutting machines come complete with a vacuum system designed to remove these waste particles and would all work extremely well if it wasn’t for the inherent static problem encountered due to the nature of the plastic film. Plastics generally have very high resistivities and this allows them to maintain static charges for long periods of time.
This means that due to the electrostatic charge, the chad remains on the material and becomes trapped between the film layers as they rewind. This has serious quality consequences as the end-user will receive contaminated stock and reject the batch, resulting in the manufacturer having to either throw away the film or rewind and remove the chad. Both options cost valuable resources and affect the bottom line.
The reason many manufacturers have chosen the Meech Series 1000 web cleaner is that it combines static eliminators, brushes and a high power vacuum dust collection system that has been designed with a unique, highly efficient vacuum control plate that gives complete coverage of the material surface. Flexible ducting then carries the contaminants to the collection system, where they are collected in a filter bag.
By using powerful ionsation, the static elimination bars will break the bond between the chad and the film, while the non-contact brushes destroy the boundary layer allowing the removal of even the smallest particles.
And it’s not just efficient operation that has manufacturers choosing the Meech Series 1000. Due to the fact that it is a non-contact system, there are no scratches on the end-product, so quality is not compromised. It is also easy to install on existing machines and Meech’s engineers have developed a number of bespoke systems to ensure that customers’ exact requirements are met.
With its low cost and trouble-free maintenance, the Meech Series 1000 ensures customers see a quick return on investment and their products are delivered contamination-free.