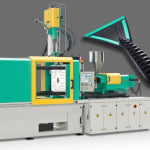
"With our multi-component injection moulding and Arburg plastic freeforming applications, we will demonstrate our expertise in efficient plastic processing – from high-volume production to one-off parts. We see great potential, particularly for such high-quality, production-efficient injection moulding machines and for industrial additive manufacturing in our market," says Dr Daniel Orel, Managing Director of Arburg spol. s r.o. in the Czech Republic. "Furthermore, we offer outstanding support and service, as well as well-founded consulting, including with regard to automation and turnkey solutions."
Expertise in multi-component injection moulding
Thanks to decades of know-how in multi-component injection moulding, Arburg has also mastered the efficient production of parts as hard/soft combinations inside out. At the MSV 2018, a two-component application will be demonstrated based on the example of ice scrapers. An Allrounder 570 S with a clamping force of 2,200 kN and two, size 400 and 170, injection units will produce the 80-gram parts. First, the machine produces the pre-moulded part from ABS using the horizontally arranged size 400 injection unit. The 1+1-cavity mould supplied by Polarform is then rotated through 180 degrees via a servo-electric indexing unit and, in this position, the TPE component is moulded on via the vertical, size 170 injection unit. In this manner, a ready-to-use finished part with a flexible lip is produced in a cycle time of around 60 seconds.Freeformer for industrial additive manufacturing
Experience with the Freeformer and Arburg Plastic Freeforming (APF) has demonstrated that, as well as prototyping, this open system is also particularly suitable for the industrial additive manufacturing of functional parts. At the MSV, the Freeformer will additively manufacture a conveyor screw for pet-feed dispensers. The complex geometries of the functional part made from PA10 are produced with the aid of an alkaline-soluble support material (Armat 21).One advantage of the APF process is that the qualified standard plastic granulates also used in injection moulding can be processed. New materials are continuously being added to the existing database of original materials. This comprises standard amorphous granulates, such as ABS, PA and PC, as well as soft TPU and semi-crystalline PP. This year, processing of the materials PMMA (Plexiglas 7N) and SEBS (CawitonPR13576) was presented for the first time.
Source: Arburg