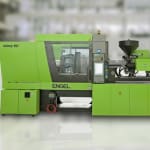
With its five exhibits the injection moulding machine maker and automation expert will be presenting turn-key solutions for highly economic manufacturing. At the same time, two other trends at this year's Chinaplas, increased precision and productivity, will also be presented.
The need to avoid aggressive use of resources is becoming increasingly important in China's manufacturing industry. In its recently published five-year plan, the Chinese government firmly established the importance of sustainability. Engel the worldwide pioneer in energy-efficient drive concepts, has taken a leading position among European machine manufacturers in Asia in this market environment. Before the end of the year, Engel will be doubling the capacity of its large-scale machine production works in Shanghai to an annual output of 200 machines in order to cope with increasing demand from China, but also from South-East Asia and India.
The Engel duo 5550/700 injection moulding machine which will be producing engine covers on a mould by Mecaplast also comes from the Shanghai works. The machine is equipped with the servohydraulic Engel ecodrive.
Engel ecodrive is available as an option for all hydraulic machines in the Engel product programme, comprises a servomotor with fixed displacement, or variable capacity pump, instead of a permanently running asynchronous motor. The machine's speed is directly linked to the drive speed. When it is at standstill, for example during the cooling phase, the machine does not consume any power.
The machine consumes up to 70 percent less energy than comparable, conventional hydraulic machines. This helps the Engel hydraulic machines to achieve energy consumption figures that can hold sway with values achieved by fully electric machines. On top of this, the ecodrive reduces cooling water consumption at the oil cooler to a minimum, in many cases even to zero. The oil temperature is an indicator of the machine's energy efficiency.
The duo machine presented in Shanghai will comprise a complete production cell including automation. A linear robot of the Engel viper 40 type will take the engine covers off the mould. The new Engel viper robot generation stands for best-in-class efficiency and productivity. Thanks to its mass identification software, the viper robot adapts the speed of its movements to match the weight of the part to be taken off. If the weight is below the rated value, the robot works more quickly.
At the same time, the vibration control software reduces vibration, thus not only ensuring improved tracking and positioning accuracy, but also achieving shorter cycle times. Wait times are also minimised, with the robot using efficiency control to automatically adapt its sequences outside of the injection moulding machine to match the cycle time of the plant. Since the K trade fair last October, the viper robots have been available in five sizes with nominal load bearing capacities of 6 to 60 kg.