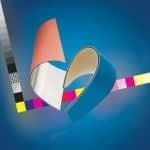
When printers start to feel uneasy if the public find out they use UV printing techniques it is high time to take action.
According to the print research association Fogra Forschungsgesellschaft Druck e.V., technical solutions which efficiently minimize or avoid the migration of photoinitiators have been on the market for years. Photoinitiators are photo-active substances which form radicals after exposure to light and trigger polymerisation. However, due to high costs the relevant colour series are not being sufficiently exploited here.
In January 2011 BASF announced a “technological breakthrough” in the form of Igracure which is based on developing cationic photoinitiators for packaging printing.
For the first time now, quick curing by UV is possible with only very low emissions, the company said. Igracure 270 is a new, high-molecular sulfonium salt which is said to fulfil the high standards that UV-curable printing on food packaging is required to meet. Extensive tests have shown that emissions and migration are both very low, say the company. A complete registration package has been put together.
The main areas of application for Igracure 270 will be in UV-curing applications that demand low-emissions such as clear overprint varnishes, flexographic inks, screen inks and inkjet inks for printing food packaging made from paperboard, plastics and metal.
The issue of chemical accumulations in food has become a huge consumer focus over the past few years, thereby also making it a focus for food producers and retail chains. Time and again the media reports on harmful substances migrating from packaging into packaged goods and significantly high levels of various photoinitiators have been found in pasta, rice, pizza dough, muesli bars and cookies, to name but a few. This news has alarmed customers and has ultimately proven highly damaging for the companies involved.
Safety is in high demand – for producers and consumers alike. The food packaging market is huge but UV printers have to meet similarly high requirements as those producing medical or cosmetic packaging and these, too, can be UV printing products. Even with a potential risk nowadays every single variable in the process can be measured and controlled thereby avoiding any possible contamination.
This issue was also the focus at Fogra’s 6th UV printing users’ forum in November of last year. It became apparent at the event that the food industry quite understandably also needs uncompromisingly safe packaging.
For Kraft Foods, for instance, special approvals are necessary when packaging is to be imprinted with UV-cured inks or varnishes.
The forum also discussed why the market does not in fact feature risk-free ink systems only. While this would mean more expensive printing inks, for the (end) user the ensuing price rise would scarcely be felt – and issues such as migration or contamination would finally be a thing of the past. However, the experts were still unable to anticipate whether it would be possible to implement such strategies on the market.
Mayr Melnhof Karton AG, for instance, uses an adapted choice of cardboard and paper qualities and suggests cardboard packages be made from fresh fibre for sensitive goods. The contamination of packed goods can result from the recycled fibre in the covering box – which means high quality specifications are also required when selecting secondary packaging.
Erroneous odours caused by UV rays during the curing process in the printing press also pose a problem: various photoinitiators generate strong-smelling decomposition products from the printing inks and the bonding agents for the paper coating made with butadiene/styrol produce an unpleasant smell when exposed to UV light, stresses the Fogra institute. Blanket washing and fountain solutions also play a role here and even the recyclability of UV prints is an issue in this context. Customers are now starting to expect the production of printed matter which is not harmful to the climate. Naturally, it will also be interesting to see whether these products, once used, will be disposable as hazardous or municipal solid waste or whether their raw materials can by recycled.
All in all, relevant solutions are already available now. However, answers as to whether, when and to what extent these solutions will replace the conventional process as yet seem a long way off.