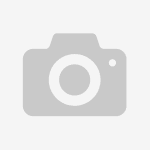
A technology to fight against the growing worldwide problem of product counterfeiting has been developed by researchers at Warwick Manufacturing Group (WMG), at the University of Warwick in the UK.
Following a three-year R&D phase, WMG is now starting the process of commercialisation with industrial partners, whose names have not yet been announced. Lead researcher Professor Gordon Smith said: - At this stage, things are moving very quickly.
The research group is not revealing full details of how the technology works, but Prof Smith told that it has been developed from work that focused on flow and turbulence effects during the injection of plastics into a mould. The in-mould process creates a "watermark" by manipulating pigment using an electro induction technique.
The watermark would be repeatable and could appear on or below the surface of the moulded product. Because the watermark is created as an intrinsic part of the plastic product as it is being moulded, it would require very detailed technical knowledge and equipment to replicate the watermark process.
Prof Smith said: - There is an enormous amount of interest in anti-counterfeiting technology for plastic products. We at the University of Warwick are working on several processes to prevent plastic components being copied and this ?in mould` process is the first of them to be developed for use.
The incentive to develop such technologies is clear from the huge scale of counterfeiting, which is estimated to represent 5-7% of world trade. The global cost of counterfeit goods (including such things as software and pharmaceuticals as well as manufactured products) is in the region of $600bn each year, according to the website of The International AntiCounterfeiting Coalition, based in Washington.
Prof Smith also said: - For commercial reasons we cannot detail collaborators but we are now exploring its use with one company that is plagued by the failure of a counterfeit plastic based safety critical product which is made to look exactly like their safety critical product and therefore damages their reputation as well as losing them sales.
There are hopes the new technology will be of interest to a range of manufacturers` products such as DVDs and other discs in the entertainment and computing markets to plastic containers used by a range of consumer industries.