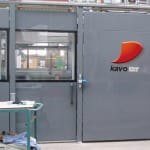
With its newly developed machine kavoblow 200/80-R2, all commonly used plastics can be processed. The machine can be used for the production of containers with a volume between five milliliters and five liters. Its highly efficient, single-stage blowing technology combines flexibility and productivity.
Günter Ausserwöger, Head of Division Kavo at Greiner Packaging, is pleased to announce: “ With our new machine we are capable of producing higher quantities of plastic bottles and containers of all types, and with greater efficiency. It is setting new benchmarks for the prices of innovative, customized products.”
The machine, developed by Greiner Packaging in tandem with Mould & Matic, is named the kavoblow 200/80-R2. It went into operation in 2011, at our location in Wartberg on the Krems river.
"The machine was developed over a period of about 18 months and both enterprises applied their main strengths to the project. Mould & Matic draws on long-term experience of more than forty years in mold construction and automation, while Greiner Packaging has gained its packaging know-how over a period of more than fifty years,“ says Ausserwöger. The result is a unique machine that works with top efficiency, setting new technological standards.
With the kavoblow 200/80-R2, all commonly used plastics can be processed. Products are produced from PET, PP, PE, PS, and PA in consistently guaranteed high quality without impact marks. In addition, the new machine stands out for its high degree of flexibility, and is utilized in the production of containers holding volumes of between five milliliters and five liters.
The kavoblow 200/80-R2 is based on an injection molding machine concept, combined with a newly developed blowing station that includes automation features. The pre-form is manufactured on a vertical machine, using the traditional injection molding system. Then, transport into the blowing station is performed using a gripping mandrel. Upon completion, the products are unloaded and stacked completely automatically.