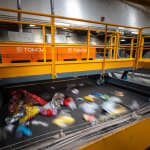
Based in Corsico in the Lombardy Region of Italy, Masotina S.p.A. operates one of Europe’s largest materials recovery facilities (MRFs) for the separation and recovery of plastic from municipal waste. The company uses 32 Autosort machines supplied by global sensor-based sorting specialist, Tomra Recycling, to sort and recover high volumes of plastics primaily from single stream household waste collections, as well as some commercial waste. Thanks to the latest generation of Tomra’s technology, Masotina is today reaping the benefits of ‘tailor-made’ plastic sorting solutions.
Masotina’s MRF was designed to treat municipal waste containing high volumes of plastic as a valuable resource, preparing it for subsequent reuse and recycling in line with the requirements of three Italian packaging and recycling consortia.
The company’s Corsico MRF boasts 32 Tomra Recycling Autosort across three lines, which together enable the plant to process 250,000 tons of post-consumer and commercial waste plastics annually.
Sebastiano Chizzali, General Manager of Masotina Spa, comments: "When Pioneer Point Partners acquired the company in 2011, it invested heavily in management and technology, enabling the group to become a leader in plastics recovery and valorization.”
In 2014, Tomra Recycling Autosort units were installed in a pre-sorting line and treatment line and later, in 2019, more units were added to support the addition of two further lines. A total of 32 Autosort are now installed at the plant.
"The plant’s design configuration is very flexible and is capabale of processing infeed material which comprises separated single stream post-consumer and commercial waste collections,” as Chizzali explains. “The lines are designed to sort and recover clean plastic fractions by both polymer and color. Sensor- based sorting technology was chosen to optimize the plant’s sorting processes. We chose Tomra as our technology partner because of the company’s reputation for innovative, sophisticated and reliable technology, all of which are fundamental requirements for a partner which provides the core technology for our business."
“Working with Tomra we have been able to develop a plastics recovery facility which we can adapt in order to meet the differing requirements of our customers,” Chizzali continues. "For us, the relationship of trust that has been established with Tomra is also important. They not only met our tight installation timeframes, but also helped us to develop and optimize our recovery processes effectively and efficiently.”
Francesca Romana Febbo, Quality, Environment and Safety Manager at Masotina, adds "We now have a considerable number of Tomra optical sorters and we are very satisfied with their performance. There are 12 units on the original line from 2014, four on the new pre-sorting line (which includes the Tetra Pak line) and 16 on the new main polymers line.”
At present, the new main polymers line can process 15tph, the historical line between 7 and 10tph, and the Tetra Pak line 4tph, giving a total plant throughput of between 26 and 29tph.
Thanks to the highly accurate sorting carried out by Tomra's Autosort units, in addition to recovering single-layer PET trays, the Masotina facility can also target and recover multilayer PET trays, with the end recovered fraction meeting the quality requirements set by Corepla for use as food-grade rPET. Corepla is Italy’s national consortium for the collection, recycling and recovery of plastic packaging.
Febbo explains: "One of the Autosort units is programmed to detect VPET (PET used in trays), allowing it to be sorted and separated from the PET used in bottles. We have found that, in addition to having the ability to accurately identify PET mono-layers, our recovery rate of both mono-layer and multi-layer PET trays has increased five fold. This is a key operational benefit for us as previously it was difficult to separate PET trays and we relied on manual sorting for this task.”