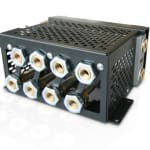
The Engel flomo has seen injection moulding machine manufacturer Engel add a temperature control and water distribution unit to its manufacturing programme since K 2010. The system, with its name based on flow monitoring, is suitable for permanent monitoring of all cooling and temperature control circuits on injection moulding machines and moulds. As it works electronically, it is an extremely economic alternative to legacy, maintenance-intensive cooling water batteries with inspection glasses.
Water is fed in from the water supply through a central inlet or from a temperature control device on the manifold, where the feed pressure and temperature are measured. The temperature measurement serves to check that the temperature control device and/or cooling system are working properly.
The flow lines are equipped with shut-off valves to allow individual circuits to be deactivated as needed. The flow rate and temperature of the water exiting the mould directly are measured in the system's return channels. The flow rates on any circuit can be set manually using the fine-adjustment regulating valves.
The pressure, temperature and flow rate signals are transferred via an interface to the injection moulding machine's control unit where they are displayed graphically and numerically, evaluated and stored for complete documentation. Engel flomo is integrated with the CC 200 control unit on the Engel injection moulding machine. In other words, the users keep their accustomed control environment rather than needing to learn how to operate the device. In addition to this, integration ensures a high level of process safety, as all quality-related parameters, including information directly from the mould, are visible at a glance.
Set values can be defined for the flow rate on the control unit. If the actual values change, e.g. due to soiling of the cooling bores in the mould, the system triggers an alarm. Leakage monitoring with automatic feed and return line cut-off is available as an option.
Compared with legacy water distributors, this also means considerable reductions in maintenance overhead. Two factors contribute to this. For one thing, the system no longer has inspection glasses, which would need to be cleaned at regular intervals; for another, the new distributors use vortex sensors that have no moving parts or water filters. This sensor type relies on an impediment in the measuring line to artificially create a vortex. Depending on the water flow volume, this creates pressure impulses which are converted by the sensor into a measuring signal proportional to the flow. Vortex sensors are more resilient to soiling than legacy turbine flow meters and this removes the need for water filters. This results in lower pressure loss on the system.
The Engel flomo is currently available as a 4x and 6x module; if needed, multiple modules can be fitted in parallel. The modules are suitable for temperatures up to 95 °C and flow rates of between 1 and 15 l/min or 2 to 40 l/min. Measuring just 280 x 240 x 134 mm or 380 x 240 x 134 mm, these distributors are among the most compact in their class, and they can be mounted directly on the mould mounting platen next to the mould. This reduces the piping overhead and thus the heat loss.
Thanks to its standardised design, the Engel flomo offers a very attractive price/performance ratio. Integrated shut-off valves on the flow line and fine-adjustment regulating valves on the return line are included as standard equipment.
Mobile displays are optionally available for the distributor systems thus boosting efficiency in larger machine farms. The display helps the machine operator during manual adjustment of the distributor on site, as it can be located at any position on the injection moulding machine.