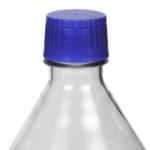
“Developing innovative solutions that can improve safety and efficiency in laboratory environments is increasingly important to the healthcare industry, enabling reduced costs and faster results. Working with TriForest Labware, we were able to develop a solution that helps answer these challenges, offering a meaningful alternative to traditional materials, which helps lab technicians culture samples with reduced risk of injury and enhanced ability to achieve real-time results. SABIC is committed to collaborating with OEMs to develop innovative technologies aimed at solving pertinent industry challenges," says Cathleen Hess, Director of Healthcare Marketing for SABIC's Innovative Plastics business.
Safety and efficiency with virtually unbreakable Lexan resin
SABIC's Lexan HP resin used in the TriForest Labware 3L flask enables enhanced safety in both the transportation of lightweight flasks, as well as their use in the lab. One of the risks associated with a traditional material like glass is its potential to break during transport, posing a risk of injury to those handling the flasks. Additionally, because the 3L flask is made from Lexan HP resin as opposed to glass, it is much less likely to break, thereby significantly lowering the risk of lab technicians being exposed to biohazardous materials that may be in the flask.Efficiency in laboratory settings is another critical industry requirement met by TriForest Labware's 3L flask. Injection blow molding with Lexan HP resin provides uniform, thicker walls enabling optical density measurement capabilities with limited pH shift. As a result of this new innovation, lab technicians can measure cultures within the closed system of the single flask accurately, increasing efficiency as the need to create smaller testing samples can be eliminated. Along with the benefit of real-time sample measurements enabled by these new flasks, the ability to withstand autoclave sterilization means the flasks can be reused multiple times, which can save costs.
"We've had a long and successful relationship with SABIC, and through our collaborative development process, we were able to identify a technology that would bring significant advantages to the healthcare industry and meet the rigorous needs of our customers," said Syed Rehan, vice president, TriForest Labware. "Without the exceptional properties provided by Lexan HP resin - optical clarity, impact resistance and the ability to be injection blow molded - we would not have been able to make this 3L Fernbach flask."
Enabling Consistent Regulatory Compliance
SABIC's Lexan HP resin is among the more-than-50 high-tech healthcare materials covered by SABIC's healthcare product policy, designed with the intent of supporting OEMs in achieving regulatory compliance for healthcare and pharmaceutical applications, saving both time and money. SABIC's healthcare product policy gives customers confidence that its materials meet global standards for safety, are available in consistently formulated supply and have been pre-assessed for biocompatibility.
SABIC will be displaying the TriForest Labware 3L flask and numerous other innovative solutions for the healthcare industry during MD&M West from February 11-13, 2014, in Anaheim, California.